Il patriottismo dell'élite industriale sovietica era combinato con la corresponsabilità per il risultato finale
L'interazione interindustriale in ogni momento - sia nell'Impero russo che nell'URSS e oggi - non apparteneva ai punti di forza dell'industria nazionale. Al contrario della Germania o degli Stati Uniti, dove gli obblighi contrattuali avevano e hanno una forza immutabile e quasi sacra.
Prendiamo, ad esempio, il rapporto tra metallurgisti russi e costruttori di macchine. Nella seconda metà del XIX secolo, i nuovi impianti di ingegneria dei trasporti e i cantieri navali non ricevevano la quantità richiesta di metalli industriali dai minatori degli Urali. Quest'ultimo considerava non redditizio produrre molti prodotti laminati relativamente economici, poiché lo stesso profitto era fornito da un volume molto più piccolo di costosa lamiera per tetti. Il metallo mancante per gli assi delle auto, gli alberi dei motori e la pelle delle navi doveva essere acquistato all'estero. Solo alla fine del secolo il problema fu risolto dagli stabilimenti metallurgici della Russia meridionale, fondati da industriali belgi o francesi. Negli Urali, i francesi costruirono anche uno stabilimento: Chusovskaya.
Sembrerebbe che in epoca sovietica tali capricci fossero fuori questione. Inoltre, gli stabilimenti metallurgici costruiti negli anni '30 fornivano al Paese tutto il metallo. Tuttavia, ogni volta che i costruttori di macchine richiedevano nuovi tipi complessi di prodotti laminati, i metallurgisti li padroneggiavano per anni o addirittura decenni.
feudalesimo dipartimentale
Passiamo alla storia di Uralvagonzavod. Già nei suoi primi progetti, era previsto l'utilizzo di ruote in acciaio laminato solido sotto le vetture a quattro assi poiché la capacità di progettazione raggiungeva la sua capacità di progettazione, il cui fornitore era previsto per il vicino stabilimento metallurgico di Novo-Tagil. Tuttavia, quest'ultimo era in costruzione dal reparto metallurgico, e rimandò la costruzione del laminatoio per ruote al 1938-1942, e non in primo luogo. Di conseguenza, il caso non iniziò prima della guerra. E dopo la guerra, il noleggio di ruote non era troppo interessato ai metallurgisti. Risultato: fino alla metà degli anni '50, le auto Tagil uscivano dalla fabbrica su ruote in ghisa di breve durata anziché su ruote in acciaio. Ciò ha portato enormi perdite ai ferrovieri, ma non c'era scelta: o tali auto o nessuna.
La stessa cosa è successa con l'introduzione degli acciai bassolegati nella costruzione di carrozze. Hanno promesso una notevole riduzione del peso proprio del materiale rotabile mantenendo tutte le caratteristiche prestazionali. I progettisti di Uralvagonzavod iniziarono a progettare automobili in metallo a bassa lega alla fine degli anni '30, ma la loro produzione in serie iniziò solo nella seconda metà degli anni '50, poiché i metallurgisti non fornivano né prodotti laminati appropriati né ferroleghe per le parti di fusione.
Va detto che il virus del feudalesimo dipartimentale ha colpito gli stessi costruttori di macchine. Nell'estate del 1937 ebbe luogo una storia interessante che caratterizzò i rapporti tra le agenzie di quel tempo. La direzione principale delle imprese metallurgiche ha inviato a Uralvagonzavod un ordine per cinquemila tonnellate di pezzi grezzi per il laminatoio di fasciature recentemente lanciato dello stabilimento di Novo-Tagil. La direzione principale dell'ingegneria dei trasporti è stata indignata per l'invasione di un'impresa subordinata. Vice Capo della Direzione Generale G. G. L'11 luglio Aleksandrov ha inviato una lettera a GUMP e Uralvagonzavod con la seguente dichiarazione: "Siamo estremamente sorpresi che la soluzione di una questione così importante come l'organizzazione della produzione di un cerotto a Uralvagonzavod sia stata effettuata senza la nostra partecipazione, e ancora di più - non ci è stata nemmeno inviata una copia dell'abito inviato a Uralvagonzavod … Vi chiedo di stabilire una procedura ferma per l'emissione di grezzi alle nostre fabbriche solo previo accordo con noi e tramite Glavtransmash."
Di conseguenza, ai metallurgisti è stato negato l'acciaio per bende, presumibilmente a causa dell'impossibilità tecnica di fondere lingotti di alta qualità nel negozio a focolare aperto dell'Uralvagonzavod. Nel frattempo, già nel 1936, qui fu fuso un pezzo grezzo assiale e nel 1937 - lingotti per laminazione di lamiere. Pertanto, i lingotti per il mulino a sudario, situato a pochi chilometri da UVZ, dovevano essere trasportati dagli impianti di Vyksa e Kuznetsk. Inoltre, la loro qualità lasciava molto a desiderare e i volumi delle forniture erano insufficienti.
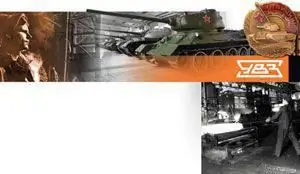
Nel 1938 la storia si ripete. Il principale consumatore di lingotti UVZ era l'impianto di artiglieria Molotov (cioè Perm), che ha ricevuto un lotto di pezzi grezzi alla fine dell'anno. E solo un piccolo numero di loro è andato al negozio di bende, che ha dovuto importare di nuovo il metallo mancante per due o duemila chilometri e mezzo. Gli interessi dell'industria nella distribuzione dell'acciaio Uralvagonzavodsk hanno chiaramente prevalso.
La malattia dipartimentale non ha risparmiato nemmeno l'industria della difesa. Numerose pubblicazioni sulla storia della costruzione di carri armati sovietici sono decisamente piene di esempi di come la costruzione di prototipi o lo spiegamento della produzione di massa siano stati ritardati a causa della mancata consegna del metallo, in particolare dell'armatura.
E anche oggi l'interesse settoriale non è andato da nessuna parte, ha solo cambiato forma. Le richieste di nuove forme di laminati vengono semplicemente respinte con prezzi esorbitanti. Non c'è bisogno di parlare di una politica coordinata. Dopo il crollo del tasso di cambio del rublo a cavallo tra il 2014 e il 2015, le aziende metallurgiche hanno aumentato i prezzi del materiale rotabile del 30-60 percento. E hanno subito iniziato a lamentarsi dei costruttori di macchine per le attrezzature che erano aumentate di prezzo - dopotutto, le macchine sono prodotte in Russia e non sono legate al tasso di cambio del dollaro.
Sembra che nel nostro Paese ci sia una sola cura per problemi trasversali: la creazione di sistemi integrati verticalmente, dove il minerale estratto dalle nostre stesse forze viene trasformato prima in metallo e poi in macchine finite.
unità in tempo di guerra
C'è, tuttavia, un breve periodo nella nostra storia in cui gli interessi dell'industria sono passati in secondo piano. Stiamo parlando della Grande Guerra Patriottica. L'indubbio patriottismo dell'élite industriale sovietica a quel tempo era combinato con la corresponsabilità di tutti coloro che erano coinvolti nella produzione della difesa per il risultato finale. Cioè, il direttore dell'impianto di laminazione corazzato era responsabile non tanto del volume di acciaio fuso e laminato, ma del numero di serbatoi costruiti.
Il passo principale in questa direzione è stato fatto dal direttore di NII-48 A. S. Zavyalov. Nei primi giorni della guerra, si rivolse al governo con una proposta per incaricare l'istituto di introdurre tecnologie per la produzione di acciai speciali e strutture corazzate presso le imprese nell'est del paese, che furono inizialmente coinvolte nella produzione di armature veicoli. All'inizio di luglio, squadre di specialisti di NII-48 hanno guidato la ristrutturazione tecnologica di 14 grandi imprese. Tra questi c'erano gli stabilimenti metallurgici di Magnitogorsk e Kuznetsk, gli stabilimenti metallurgici di Novo-Tagil e Chusovka, l'impianto di costruzione di macchine pesanti degli Urali, il Gorky Krasnoye Sormovo, lo stabilimento di trattori di Stalingrado, l'ottobre rosso di Stalingrado e il n. 264. Pertanto, Zavyalov ha violato il tabù anteguerra: l'elenco comprendeva le imprese di tre commissariati del popolo.
Il patriottismo e la soppressione forzata dell'egoismo dipartimentale fornirono alla metallurgia sovietica tassi di sviluppo dei prodotti della difesa senza precedenti, né nel periodo prebellico né nel dopoguerra. In pochi mesi, nell'est del paese (principalmente negli Urali), fu organizzata la produzione di ferromanganese, ferrosilicio, ferrocromo, ferrovanadio e altre leghe, senza le quali è impossibile ottenere l'acciaio per armature. Dopo la perdita delle regioni occidentali, Chelyabinsk rimase l'unico impianto di ferroleghe nell'URSS. Su di essa, in breve tempo, la fusione fu aumentata di due volte e mezzo. Sono stati prodotti 25 tipi di prodotti, ma soprattutto di vari tipi di ferrocromo. La fusione del ferromanganese è stata stabilita negli altiforni, e non solo nei vecchi altiforni a basso tonnellaggio degli impianti di Nizhniy Tagil e Kushvinsky, ma anche in un grande forno moderno della Magnitogorsk Combine. Contrariamente a tutte le idee prebelliche, il ferrocromo fu fuso nella seconda metà del 1941 nei loro altiforni dai metallurgisti degli impianti di Nizhniy Tagil e Serov, e gli scienziati del ramo degli Urali dell'Accademia delle scienze dell'URSS fornirono grande assistenza nella creazione di un nuovo tecnologia. Successivamente, la fusione del ferrosilicio fu padroneggiata negli altiforni di Serov.
Non c'erano campi corazzati né negli Urali né nella Siberia occidentale prima della guerra, dovettero essere frettolosamente trasferiti dalle imprese che si trovavano nella zona di combattimento.
Nell'estate del 1941, l'attrezzatura evacuata era ancora in transito. E poi il capo meccanico della mietitrebbia Magnitogorsk N. A. Ryzhenko suggerì di far rotolare l'armatura su un mulino in fiore. Nonostante il grande rischio, l'idea è stata realizzata. E in ottobre è entrato in servizio un campo blindato, prelevato dallo stabilimento di Mariupol. È stato montato in soli 54 giorni. Secondo gli standard prebellici, ci volle un anno.
Lo stabilimento di Novo-Tagil ha ottenuto il campo da Leningrado. I preparativi per la sua ammissione sono iniziati a luglio, inizialmente si presumeva che sarebbe stato montato sul sito della benda. Il campo delle bende è stato smontato, ma si è scoperto che il vecchio stock non era sufficiente per installare il campo blindato e doveva essere posizionato altrove. La guerra ha costretto a fare ciò che fino a poco tempo fa era considerato impossibile: solo un anno fa, i tentativi di realizzare costruzioni industriali con un metodo integrato "ad alta velocità" a Nizhny Tagil hanno avuto al massimo un successo parziale, e nell'estate del 1941 il più l'operazione di costruzione complessa era quasi perfetta. Il 10 settembre, la prima lamiera di acciaio Tagil è stata laminata un mese prima del previsto. In totale, entro la fine dell'anno, sono state ottenute 13.650 tonnellate di lamiera, incluso circa il 60 percento di armature (il mulino è stato testato su acciaio al carbonio e in ottobre - dicembre, l'acciaio al carbonio è stato laminato con una carenza di lingotti di armatura). Di conseguenza, già nel gennaio 1942, la produzione mensile di piastre corazzate nelle fabbriche degli Urali ha superato i sei mesi nell'intera Unione Sovietica prebellica.
Eventi non meno sorprendenti si sono verificati presso altre imprese poco conosciute. Durante la guerra, lo stabilimento metallurgico di Zlatoust era inferiore alla mietitrebbia Magnitogorsk in termini di volume di acciaio fuso e laminato, ma lo superava significativamente nel suo mix di prodotti: qui venivano prodotti circa 300 gradi di lega e acciaio al carbonio. Senza le forniture di Zlatoust, la produzione di molti tipi di armi, principalmente motori per carri armati, si sarebbe interrotta.
Le vecchie fabbriche degli Urali si sono rivelate indispensabili nella produzione di piccoli lotti di acciaio particolarmente pregiato. Ad esempio, il metallo di Serov Metallurgical, il principale produttore di prodotti laminati calibrati, è stato investito in ogni carro armato sovietico. Lo stabilimento di Nizhnesalda passò alla fusione del ferro e dell'acciaio di nichel. Questo elenco può essere continuato all'infinito: durante gli anni della guerra, ovunque ci fosse almeno una cupola, il metallo per armi veniva fuso.
C'è una storia curiosa con i flussi per la saldatura automatica. Prima e all'inizio della guerra, furono fusi in una delle imprese del Donbass, dopo la cui occupazione le forniture centralizzate si fermarono completamente. Alla fine del 1941, i dipendenti dell'Istituto di saldatura elettrica dell'Accademia delle scienze della SSR ucraina iniziarono a cercare materiali sostitutivi disponibili negli Urali in condizioni più o meno utilizzabili. E li hanno trovati - sotto forma di scorie di altoforno dell'impianto metallurgico di Ashinskiy. Sono stati necessari solo piccoli miglioramenti: gli altiforni hanno arricchito le loro scorie con manganese e quindi le hanno trasformate in un flusso completamente adatto. L'attrezzatura necessaria per i test è stata portata da Nizhny Tagil direttamente ad Asha.
Esempi di cooperazione locale tra serbatoio e impianti metallurgici sono molto indicativi. Prima del lancio delle proprie strutture, il trattamento termico delle parti del serbatoio dell'Ural Tank Plant n. 183 è stato effettuato presso l'impianto metallurgico di Nizhniy Tagil.
Il lavoro di successo dei lavoratori della fonderia UTZ è stato notevolmente facilitato dall'assistenza del vicino impianto di argilla refrattaria Nizhniy Tagil, che ha stabilito la produzione di tappi di selce refrattari di alta qualità. Ciò ha permesso di eseguire senza problemi la colata di fusioni di acciaio per armature pesanti per la colata sagomata.
Nel 1942-1945, i forni a focolare aperto dell'UTZ funzionavano principalmente con il gas di cokeria e altoforno proveniente dalle centrali di cokeria Novo-Tagil e Nizhniy Tagil. Il gasdotto è in funzione dal febbraio 1942. La centrale di produzione del gas dell'impianto n. 183 ha fornito non più del 40 percento del fabbisogno.
A volte bastava un semplice consiglio per risolvere un problema. Le informazioni dei metallurgisti locali su una piccola miniera di manganese sviluppata nel 1870 hanno aiutato a sopravvivere diverse settimane prima dell'inizio delle consegne di ferromanganese senza interrompere la colata dei binari dei serbatoi.
Un altro esempio: con l'aumento della produzione di acciaio corazzato, il negozio a focolare aperto non poteva più tenere il passo con la fusione del metallo per le teste delle bombe aeree. Non è stato possibile prenderlo dall'esterno. Il regista Yu. E. Maksarev ha ricordato il corso di ulteriori eventi nelle sue memorie: Quando ero a una delle riunioni del comitato cittadino, ho incontrato il direttore del vecchio stabilimento ancora Demidov e ho chiesto di prendere da me il casting di le teste delle bombe. Ha detto: non posso aiutare con l'acciaio, ma con i consigli aiuterò. E quando sono arrivato nel suo stabilimento, mi ha mostrato un convertitore Bessemer da una tonnellata e mezzo con un volume medio. Mi ha dato i disegni e mi ha detto che sa che abbiamo una buona fonderia meccanizzata e che i vostri convertitori salderanno”. Così apparve l'ordine per l'impianto dell'8 settembre 1942 sull'organizzazione nel negozio di ruote Griffin della sezione Bessemer di tre piccoli convertitori (una tonnellata e mezza di metallo ciascuno). Entro il 25 settembre, il progetto è stato preparato dal dipartimento di progettazione e tecnologia della gestione della costruzione del capitale, gli specialisti del dipartimento del capo meccanico hanno rapidamente saldato convertitori e caldaie - serbatoi di stoccaggio di ferro liquido. La corsa di prova del reparto Bessemer e la colata di un lotto sperimentale di cinque nomi di parti avvennero a cavallo tra ottobre e novembre 1942. La produzione in serie è iniziata alla fine di novembre.
Alla fine dell'argomento: la cooperazione di metallurgisti e costruttori di carri armati in tempo di guerra ha agito in entrambe le direzioni. Gli installatori dell'impianto di cisterne degli Urali hanno partecipato alla messa in servizio di molte nuove unità dell'impianto metallurgico di Novo-Tagil. Nel maggio 1944, nell'officina di fusione della torre blindata, fu prodotto un numero significativo di lastre di rivestimento per la riparazione dell'altoforno.
Ma l'assistente principale dei metallurgisti era, ovviamente, l'impianto di costruzione di macchine pesanti degli Urali. I libri degli ordini per UZTM per il 1942-1945 sono letteralmente pieni di documenti sulla produzione di pezzi di ricambio e dispositivi per scopi metallurgici, sia per le esigenze dell'industria dei carri armati che per le imprese del Commissariato popolare della metallurgia ferrosa. Nell'autunno del 1942, presso l'UZTM fu ufficialmente ripristinata una divisione speciale per la produzione di attrezzature per impianti metallurgici. Ha ricevuto il codice "Divisione 15" ed era subordinato al vicedirettore per i negozi di approvvigionamento e la produzione di scafi.
Successo all'incrocio dei settori
La collaborazione di metallurgisti e costruttori di serbatoi ha portato alla creazione di una serie di tecnologie che, senza esagerare, possono essere definite vere scoperte scientifiche e tecniche.
Dopo aver fuso e laminato l'acciaio per armature in fogli, i metallurgisti hanno trasferito i loro prodotti alla produzione di scafi blindati. Qui il metallo è stato tagliato secondo il modello nelle parti corrispondenti. Nella produzione di "trentaquattro" in particolare molti problemi sono stati causati da due parti dello scafo: i parabordi (il lato inclinato del lato) e la piastra laterale verticale. Entrambi erano lunghi, anche in larghe strisce con tagli obliqui lungo i bordi.
L'idea si è spontaneamente suggerita di arrotolare una striscia metrica di larghezza pari ai pezzi finiti. Fu formulato per la prima volta dalle autoblindo dello stabilimento di Mariupol nell'estate del 1941. Per la laminazione di prova, abbiamo scelto un laminatoio per lastre a Zaporizhstal, dove sono stati inviati due scaglioni di lingotti per armature. Ma poi non ebbero il tempo di mettersi al lavoro: le truppe tedesche che avanzavano catturarono sia i gradi che la stessa Zaporozhye.
A cavallo del 1941-1942, durante l'evacuazione e lo sviluppo della produzione di armature nelle nuove fabbriche, non c'era abbastanza striscia. Tuttavia, nel maggio 1942, il Commissariato popolare della metallurgia ferrosa ricevette nuovamente l'ordine di affittarlo per i carri armati T-34 e KV. Il compito si è rivelato difficile: le tolleranze in larghezza non devono superare -2 / + 5 millimetri, la forma a mezzaluna (curva) per la lunghezza totale della parte era di 5 millimetri. Non erano ammesse crepe, tramonti e delaminazione ai bordi in modo che la saldatura potesse essere eseguita senza lavorazioni meccaniche o taglio a fiamma.
Il lavoro sperimentale è iniziato contemporaneamente nelle officine di laminazione degli impianti metallurgici di Magnitogorsk e Kuznetsk, all'inizio senza particolari risultati. Il noleggio di parti per i carri armati KV fu presto abbandonato, ma il T-34 ebbe finalmente successo. Il team di autori composto dal capo del dipartimento metallurgico della NII-48 G. A. Vinogradov, l'ingegnere capo del KMK L. E. Vaisberg e l'ingegnere dello stesso impianto S. E. stand "900" del mulino ferroviario e strutturale è completamente nuovo metodo di rotolamento "sul bordo". Nel gennaio 1943 furono emesse 280 strisce, nel febbraio - 486, nel marzo - 1636 pezzi. Ad aprile, dopo tutti i test richiesti, è iniziato lo sviluppo della produzione lorda di strisce di misurazione per i rivestimenti dei passaruota dei serbatoi T-34. Inizialmente, sono stati forniti a UZTM e all'Ural Tank Plant, e poi ad altre fabbriche - produttori di serbatoi T-34. Il rottame, che originariamente era del 9,2%, era sceso al 2,5% nell'ottobre 1943 e le strisce scadenti furono utilizzate per realizzare parti più piccole.
Una valutazione completa e accurata della nuova tecnologia è data dal corrispondente rapporto di TsNII-48 del 25 dicembre 1943: "Un metodo fondamentalmente nuovo per arrotolare un'ampia striscia corazzata" sul bordo "è stato sviluppato, testato e introdotto nella produzione lorda, che era considerato irrealizzabile fino a poco tempo fa in URSS e all'estero. L'ottenimento di una striscia calibrata (misurata) con una larghezza della parte finita dello scafo corazzato del carro armato T-34 ha permesso alle fabbriche NKTP di adottare una nuova tecnologia ad alte prestazioni per la produzione di parti corazzate senza tagliare i bordi longitudinali. Grazie all'applicazione del nuovo metodo a una delle principali parti corazzate del carro T-34 (parafanghi), è stato ottenuto un risparmio di tempo molto significativo (circa il 36%) durante il loro taglio. Risparmio di acciaio per armature 8C fino al 15% e risparmio di ossigeno di 15.000 mc per 1000 scafi”.
Entro la fine del 1943, il rotolamento di una striscia di misurazione fu padroneggiato per un'altra parte dello scafo T-34: la parte verticale del lato. Resta solo da aggiungere che gli autori di questa invenzione hanno ricevuto il Premio Stalin per il 1943.
Nello stesso 1943, grazie agli sforzi congiunti del laboratorio dell'Istituto ucraino dei metalli (diretto da PA Aleksandrov) e dei lavoratori della Combinazione metallurgica di Kuznetsk e dell'impianto di cisterne degli Urali, fu sviluppato e padroneggiato uno speciale profilo periodico laminato nella produzione per l'approvvigionamento di massa e parti critiche dei "trentaquattro" - assi di bilanciamento. Il primo lotto sperimentale di un profilo periodico fu ricevuto a KMK a dicembre, all'inizio del 1944 iniziò la produzione in serie. Ad ottobre, l'Ural Tank Plant è passato completamente alla produzione di assi di bilanciamento da un nuovo grezzo, alla fine dell'anno UZTM si è unito a esso. Di conseguenza, la produttività dei martelli di forgiatura è aumentata del 63% e il numero di rotture dei pezzi è diminuito.
Il successo del lavoro dei costruttori di serbatoi è stato notevolmente facilitato dal materiale rotabile del laminatoio per bende dello stabilimento metallurgico di Novo-Tagil. A partire dalla primavera del 1942, hanno fornito spalline arrotolate con indennità di lavorazione ridotte, nel 1943 le indennità sono state nuovamente ridotte. In combinazione con il nuovo utensile da taglio, ciò ha permesso di eseguire la rimozione degli spallacci, che richiede tempo, rigorosamente nei tempi previsti e senza molto stress. Un caso raro: il commissario popolare dell'industria dei carri armati V. A. Malyshev, nel suo ordine del 28 settembre 1943, ritenne necessario esprimere una speciale gratitudine ai metallurgisti Tagil.
E infine, l'ultimo esempio: nel 1943, i cerchi dei serbatoi di supporto T-34, prima nello stabilimento di Chelyabinsk Kirov, e poi in altre imprese, iniziarono a essere realizzati con prodotti laminati profilati speciali. Questo successo è stato anche notato nell'ordine di V. A. Malyshev.
Resta da aggiungere che gli specialisti della società americana "Chrysler", dopo aver studiato il carro armato T-34-85 catturato in Corea, hanno notato in particolare la perfezione degli spazi vuoti in acciaio da cui è stato realizzato il veicolo da combattimento. E anche il fatto che spesso superavano in numero i prodotti delle imprese metallurgiche statunitensi.