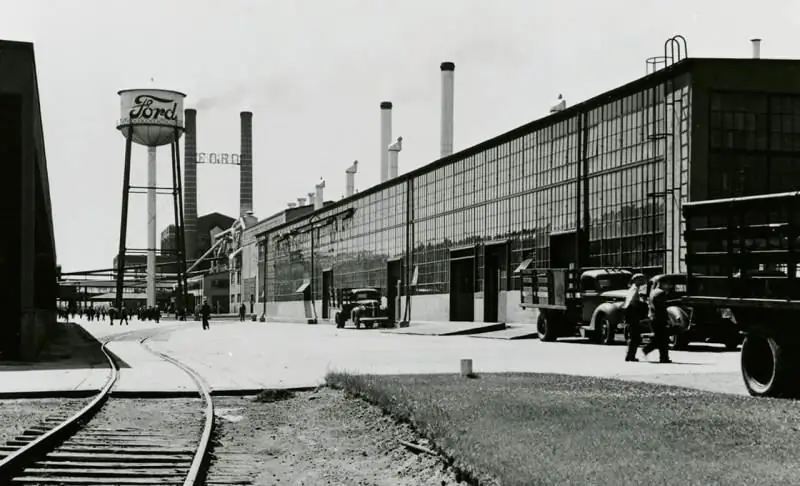
Tecnologie strategiche
Prima di conoscere le caratteristiche della produzione corazzata nello stabilimento Ford del Michigan a Detroit (USA), vale la pena spiegare brevemente le condizioni in cui si stava affermando l'industria corazzata in URSS. Come sai, tutto si impara per confronto.
La produzione di armature durante la seconda guerra mondiale era uno dei fattori più importanti per il vantaggio strategico. Con l'inizio della guerra, l'Unione Sovietica si trovò in una posizione disastrosa: tutta la produzione di blindati era concentrata nella parte europea del paese. La rapida avanzata dell'esercito tedesco potrebbe paralizzare completamente la produzione di armature per carri armati nel paese. Solo a costo di incredibili sforzi per evacuare parte delle fabbriche a est all'inizio della guerra è stato possibile ripristinare la produzione di armature. Le principali "fabbriche blindate" erano gli stabilimenti metallurgici di Kuznetsk, Nizhny Tagil e Magnitogorsk.
Ma la questione non si limitava a un semplice trasferimento della produzione in un nuovo sito dietro la linea del fronte. La maggior parte delle nuove fabbriche non era adatta alla fusione dell'armatura dei carri armati: prima della guerra, le fabbriche lavoravano per le esigenze del Commissariato popolare della metallurgia ferrosa. Wartime ha aggiunto i propri aggiustamenti. Ora i forni a focolare aperto avevano spesso lavoratori poco qualificati, c'era un grave problema della mancanza di speciali attrezzature termiche, di pressatura e di lavorazione dei metalli. Pertanto, il trasferimento della produzione di armature è stato accompagnato da una seria ristrutturazione della tecnologia stessa per la fusione dell'acciaio militare. È stato quindi necessario adeguare la produzione ai principali forni a focolare aperto per 120-180 tonnellate, escludendo il processo di disossidazione per diffusione. L'indurimento delle piastre dell'armatura e delle parti dell'armatura doveva essere effettuato in acqua.
Una tale semplificazione non poteva che incidere sulla qualità dell'armatura ricevuta. Ciò è particolarmente vero per l'acciaio 8C per serbatoi ad alta durezza più difficile da produrre. I primissimi campioni di armature durante i test hanno mostrato un'ardesia significativa e una stratificazione della frattura, un'elevata tendenza alla formazione di crepe durante la saldatura e il raddrizzamento. Oltre a ciò, i test sul campo hanno rivelato l'eccessiva fragilità dei campioni di armature durante il fuoco dei proiettili.
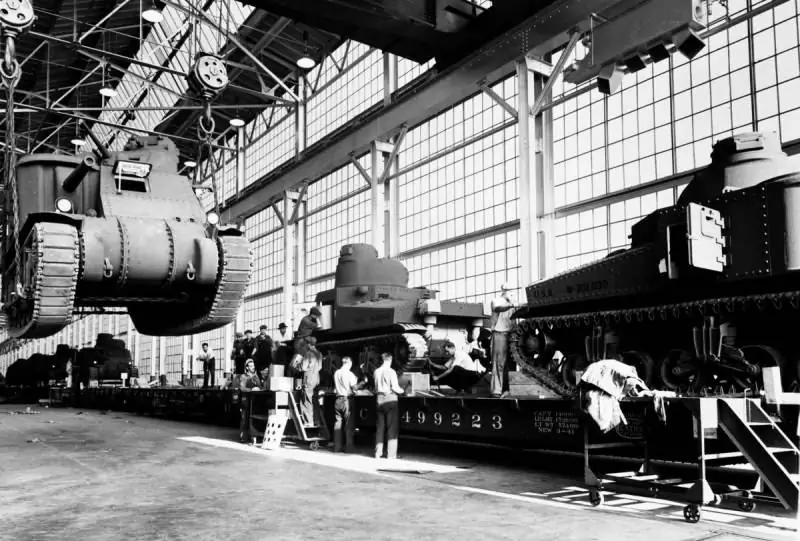
Tali difetti non potevano essere ignorati. E nel TsNII-48 specializzato hanno sviluppato una serie di miglioramenti. Prima di tutto, d'ora in poi, l'acciaio per armature doveva essere fuso solo in forni preriscaldati dopo la fusione di tipi di acciaio "civili". L'acciaio doveva bollire nel bagno di fusione a focolare aperto per almeno un'ora e mezza, e versato in stampi quadrati o convessi. Inoltre, i metallurgisti hanno prestato particolare attenzione al contenuto di zolfo nella ghisa originale (non più dello 0,06%), nonché al carbonio e al manganese. In combinazione con altre misure, ciò ha permesso di migliorare la qualità dell'armatura. In particolare, per ridurre l'ardesia e la stratificazione della frattura.
Un problema importante era la tecnologia del trattamento termico dell'armatura domestica. Per dirla semplicemente, l'indurimento e il rinvenimento delle piastre dell'armatura richiedevano troppo tempo ed energia e mancava l'attrezzatura necessaria. Era necessario semplificare il processo. A questo proposito, faremo un esempio tipico. Nel 1942, i metallurgisti di TsNII-48 riuscirono a semplificare il processo di preparazione termica così tanto che solo per parti del fondo dei serbatoi KV e T-34 risparmiarono circa 3230 ore di forno per 100 scafi.
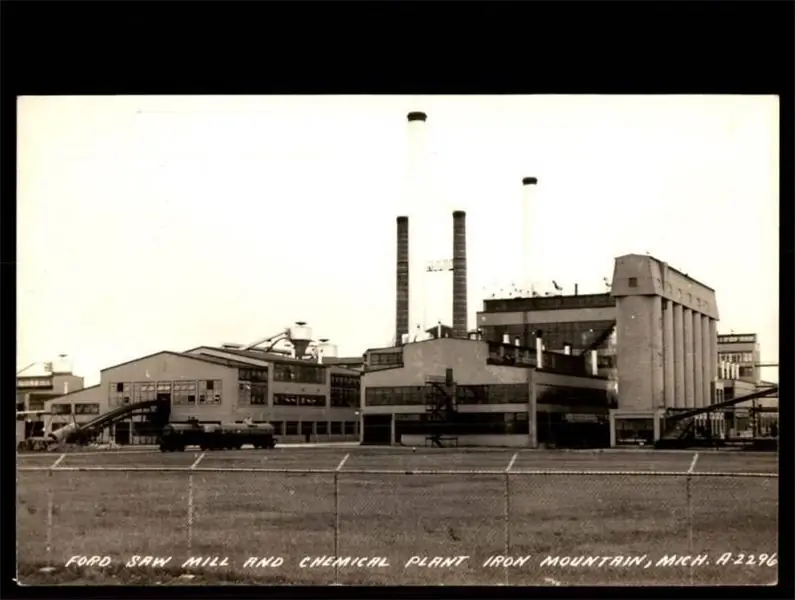
Tuttavia, fino alla fine della guerra in Unione Sovietica, le condizioni per la produzione di corazze per carri armati strategicamente importanti erano tutt'altro che necessarie. Lo stesso non si può dire dell'industria militare del partner estero, il cui territorio non è stato colpito dalla guerra mondiale. Gli ingegneri metallurgici sovietici dovettero accertarsene ancora una volta il 26 febbraio 1945, 72 giorni prima della Vittoria.
lusso americano
La storia poco nota della visita della delegazione sovietica alla fabbrica blindata Ford di Detroit è stata annunciata da Vasily Vladimirovich Zapariy, candidato di scienze storiche dell'Istituto di storia e archeologia del ramo degli Urali dell'Accademia delle scienze russa. Il materiale dello scienziato si basa sul rapporto dei metallurgisti sovietici sui risultati di un viaggio negli Stati Uniti conservato nell'Archivio di Stato russo dell'economia (RGAE). Va notato che l'RGAE è solo un tesoro di documenti d'archivio dell'era della Grande Guerra Patriottica relativi alla produzione di attrezzature e attrezzature militari. Resta solo da indovinare quanti altri segreti l'archivio conserva nelle prove finora classificate.
Secondo gli ingegneri tornati da Detroit, l'officina blindata dello stabilimento Ford era un edificio composto da due campate di 273 metri di lunghezza, 30 metri di larghezza e circa 10 metri di altezza. Allo stesso tempo, il negozio non odorava di armature. Era principalmente destinato al trattamento termico e al taglio dell'acciaio. Ciò ha naturalmente suscitato particolare interesse tra i metallurgisti sovietici, dati i problemi sopra descritti della produzione corazzata nazionale. Il principale profilo di produzione dell'officina Ford Motors era lavorare con armature fino a 76 mm di spessore. Lamiere d'acciaio trattate termicamente sono state utilizzate per saldare gli scafi dei veicoli corazzati leggeri e medi in altre fabbriche di Detroit.
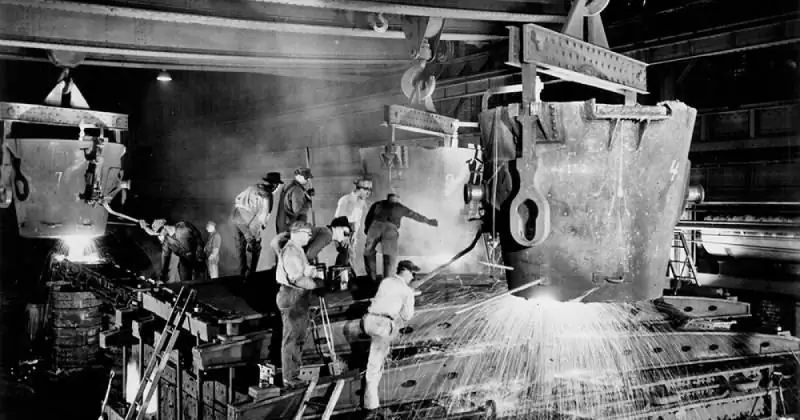
Innanzitutto, la meccanizzazione del processo produttivo ha impressionato le officine Ford. Dopo la fusione e la laminazione, le armature sono state consegnate all'officina di trattamento termico su caricatori idraulici da tavolo United. I caricatori, a loro volta, prendevano l'armatura dalle piattaforme ferroviarie situate vicino all'officina. Nell'officina stessa erano presenti due carroponti progettati per movimentare le lamiere blindate durante tutte le operazioni tecnologiche, ad eccezione dei processi di tempra.
Per creare la necessaria struttura cristallina dell'armatura, sono state chiamate due presse, con uno sforzo di 2500 tonnellate ciascuna, cinque forni metodici a nastro trasportatore di 70 metri e cinque forni a nastro trasportatore di tempra a gas da 100 metri. L'acqua veniva fornita alle presse per l'indurimento delle armature attraverso il funzionamento di sei pompe contemporaneamente, pompando oltre 3700 litri al minuto. Come hanno scritto gli ingegneri russi, la complessità e il costo della progettazione di tali presse, in grado di stampare e raffreddare contemporaneamente armature roventi, erano proibitivi. Allo stesso tempo, c'erano dubbi sull'opportunità di utilizzare presse per armature con uno spessore di 30-76 mm. Qui è emersa l'intensità dell'approvvigionamento idrico per il raffreddamento.
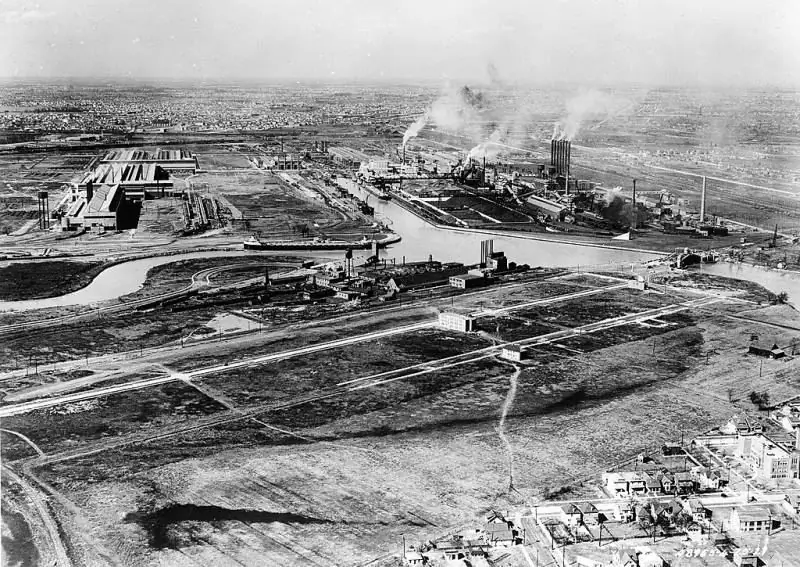
Le presse da 2.500 tonnellate non erano le uniche nel veicolo blindato Ford. Le presse Toledo # 206 erano impegnate nel taglio di armature sottili e sviluppavano una pressione di 161 tonnellate. Per armature più spesse di 2,5 cm, è stato utilizzato esclusivamente il taglio a fuoco.
Durante una visita all'impresa, i metallurgisti sono stati in grado di cogliere il processo di indurimento della sottile armatura antiproiettile. È rimasto sotto una pressa da 1000 tonnellate per 15 secondi, quindi il foglio è stato inviato per 2,5 ore per la tempra a 900 gradi Celsius e per quattro ore di vacanza a 593 gradi.
Tutta questa ricchezza tecnica è stata osservata dagli ingegneri sovietici, senza contare vari "piccoli accessori": saldatrici, fresatrici, forbici e simili.
La caratteristica principale del trattamento termico dell'armatura era il flusso continuo di produzione. In quasi tutte le fasi della lavorazione, le lamiere d'acciaio erano in fase di movimento su rulliere e trasportatori a catena. Il trasportatore era controllato da una console centrale. In una delle ultime fasi, tutte le piastre dell'armatura sono state ispezionate per il livello di durezza Brinell. In questo caso, la fluttuazione del parametro di prova da foglio a foglio dovrebbe essere minima, non più di 0,2 mm.
Di particolare interesse per la delegazione sovietica erano due macchine granigliatrici, che pulivano le piastre dell'armatura quasi dopo ogni operazione tecnologica. Un tale perfezionismo e un tale lusso potevano essere concessi solo dagli americani, lontani dalle difficoltà del tempo di guerra.