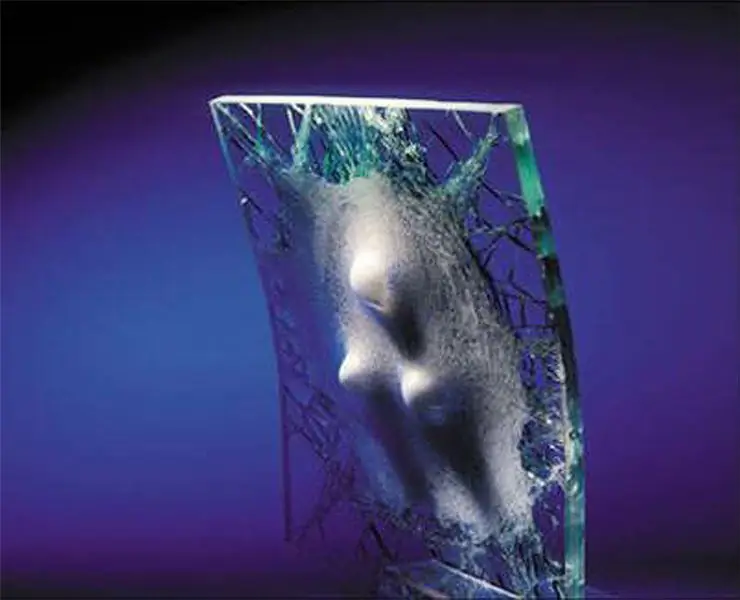
I veicoli militari sono stati tradizionalmente realizzati in acciaio per armature pesanti, costosi ma ad alta resistenza. I moderni materiali compositi ceramici sono sempre più utilizzati come protezione non portante per veicoli da combattimento. I principali vantaggi di tali materiali sono un costo significativamente inferiore, una migliore protezione e una riduzione del peso di oltre la metà. Considera i moderni materiali ceramici di base utilizzati oggi per la protezione balistica
Grazie alla sua capacità di resistere a temperature molto elevate, significativamente superiori a quella dei metalli, durezza, massima resistenza specifica e rigidità specifica, la ceramica è ampiamente utilizzata per la produzione di rivestimenti per motori, componenti di razzi, taglienti di utensili, speciali trasparenti e scudi opachi, che, ovviamente, sono tra i settori prioritari per lo sviluppo dei sistemi militari. Tuttavia, in futuro, l'ambito della sua applicazione dovrebbe ampliarsi in modo significativo, poiché nell'ambito della ricerca e dello sviluppo condotti in molti paesi del mondo, vengono ricercati nuovi modi per aumentare la plasticità, la resistenza alle crepe e altre proprietà meccaniche desiderabili da combinando una base ceramica con fibre di rinforzo nei cosiddetti materiali compositi a matrice ceramica (KMKM). Inoltre, le nuove tecnologie di produzione consentiranno la produzione in serie di prodotti trasparenti molto resistenti e di alta qualità di forme complesse e grandi dimensioni da materiali che trasmettono onde visibili e infrarosse. Inoltre, la realizzazione di nuove strutture mediante la nanotecnologia consentirà di ottenere materiali durevoli e leggeri, resistenti al surriscaldamento, chimicamente resistenti e, allo stesso tempo, praticamente indistruttibili. Questa combinazione di proprietà è oggi considerata mutuamente esclusiva e quindi molto interessante per applicazioni militari.
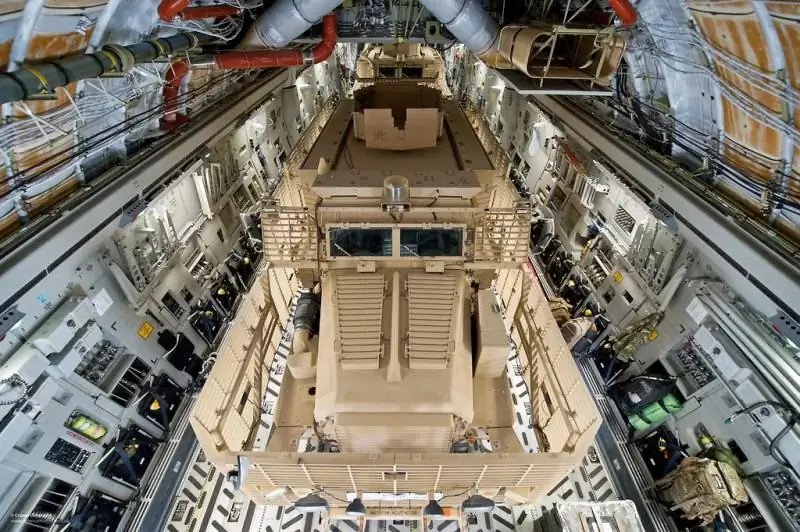
Materiali compositi a matrice ceramica (KMKM)
Come i loro analoghi polimerici, i CMC sono costituiti da una sostanza di base, chiamata matrice, e un riempitivo rinforzante, che è costituito da particelle o fibre di un altro materiale. Le fibre possono essere continue o discrete, orientate in modo casuale, disposte ad angoli precisi, intrecciate in modo speciale per ottenere una maggiore resistenza e rigidità in determinate direzioni o distribuite uniformemente in tutte le direzioni. Tuttavia, qualunque sia la combinazione di materiali o l'orientamento delle fibre, il legame tra la matrice e il componente di rinforzo è fondamentale per le proprietà del materiale. Poiché i polimeri sono meno rigidi del materiale che li rinforza, il legame tra la matrice e le fibre è solitamente abbastanza forte da consentire al materiale di resistere alla flessione nel suo insieme. Tuttavia, nel caso di CMCM, la matrice può essere più rigida delle fibre di rinforzo in modo che la forza di adesione, ottimizzata in modo simile per consentire una leggera delocalizzazione della fibra e della matrice, aiuti ad assorbire l'energia dell'impatto, ad esempio, e prevenire lo sviluppo di crepe che altrimenti porterebbe a una fragile distruzione e scissione. Ciò rende il CMCM molto più viscoso rispetto alla ceramica pura, e questa è la più importante delle proprietà delle parti mobili ad alto carico, ad esempio parti di motori a reazione.
Pale della turbina leggere e calde
Nel febbraio 2015, GE Aviation ha annunciato prove di successo di quello che definisce "il primo kit CMC non statico al mondo per un motore aeronautico", sebbene la società non abbia rivelato i materiali utilizzati per la matrice e il materiale di rinforzo. Si tratta di pale di turbina a bassa pressione in un modello sperimentale del motore turbofan F414, il cui sviluppo ha lo scopo di fornire un'ulteriore conferma della conformità del materiale ai requisiti dichiarati per il funzionamento a carichi d'urto elevati. Questa attività fa parte dell'Adaptive Engine Technology Demonstrator (AETD) Next Generation Self-Adaptive Engine Demonstration Program, in cui GE sta collaborando con l'US Air Force Research Laboratory. L'obiettivo del programma AETD è fornire tecnologie chiave che potrebbero essere implementate nei motori dei caccia di sesta generazione e, a partire dalla metà degli anni 2020, nei motori dei velivoli di quinta generazione, come l'F-35. I motori adattivi saranno in grado di regolare il loro aumento di pressione e il rapporto di bypass in volo per ottenere la massima spinta durante il decollo e in combattimento, o la massima efficienza del carburante in modalità di volo da crociera.
L'azienda sottolinea che l'introduzione di parti rotanti in CMC nelle parti "più calde e più caricate" di un motore a reazione rappresenta un significativo passo avanti, poiché in precedenza la tecnologia consentiva di utilizzare CMC solo per la produzione di parti fisse, ad esempio un mantello della turbina ad alta pressione. Durante i test, le pale della turbina KMKM nel motore F414 hanno attraversato 500 cicli, dal regime minimo alla spinta al decollo e ritorno.
Le pale della turbina sono molto più leggere delle tradizionali lame in lega di nichel, il che ha permesso ai dischi metallici a cui sono attaccate di essere più piccoli e leggeri, ha affermato la società.
“Il passaggio dalle leghe di nichel alla ceramica rotante all'interno del motore è davvero un grande balzo in avanti. Ma è pura meccanica , ha affermato Jonathan Blank, capo di CMC e leganti polimerici presso GE Aviation. - Le lame più leggere creano meno forza centrifuga. Ciò significa che è possibile restringere dischi, cuscinetti e altre parti. KMKM ha permesso di apportare cambiamenti rivoluzionari nella progettazione di un motore a reazione”.
L'obiettivo del programma AETD è ridurre il consumo specifico di carburante del 25%, aumentare l'autonomia di volo di oltre il 30% e aumentare la spinta massima del 10% rispetto ai caccia di quinta generazione più avanzati. "Una delle maggiori sfide nel passaggio da componenti CMC statici a componenti rotanti è il campo di stress in cui devono operare", ha affermato Dan McCormick, Advanced Combat Engine Program Manager di GE Aviation. Allo stesso tempo, ha aggiunto che testare il motore F414 ha prodotto risultati importanti che verranno utilizzati nel motore a ciclo adattivo. “Una pala di turbina CMC a bassa pressione pesa tre volte meno della pala metallica che sostituisce, inoltre, nella seconda modalità economica, non è necessario raffreddare la pala CMC con aria. La pala sarà ora più efficiente dal punto di vista aerodinamico in quanto non è necessario pompare tutta questa aria di raffreddamento attraverso di essa".
I materiali KMKM, in cui l'azienda afferma di aver investito più di un miliardo di dollari da quando ha iniziato a lavorarci sopra nei primi anni '90, possono resistere a temperature di centinaia di gradi superiori alle tradizionali leghe di nichel e si distinguono per il rinforzo in fibra di carburo di silicio a matrice ceramica., che ne aumenta la resistenza all'urto e la resistenza alla rottura.
GE sembra aver svolto un lavoro piuttosto duro su queste pale di turbina. In effetti, alcune delle proprietà meccaniche di KMKM sono molto modeste. Ad esempio, la resistenza alla trazione è paragonabile alla resistenza alla trazione del rame e delle leghe di alluminio economiche, che non è molto buona per le parti soggette a grandi forze centrifughe. Inoltre, mostrano una bassa deformazione alla rottura, cioè si allungano molto leggermente alla rottura. Tuttavia, queste carenze sembrano essere state superate e il peso ridotto di questi materiali ha sicuramente dato un contributo importante alla vittoria della nuova tecnologia.
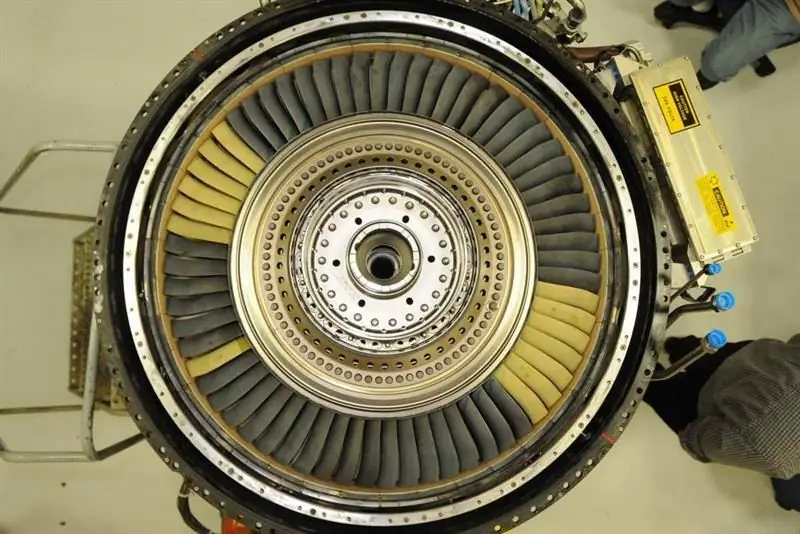
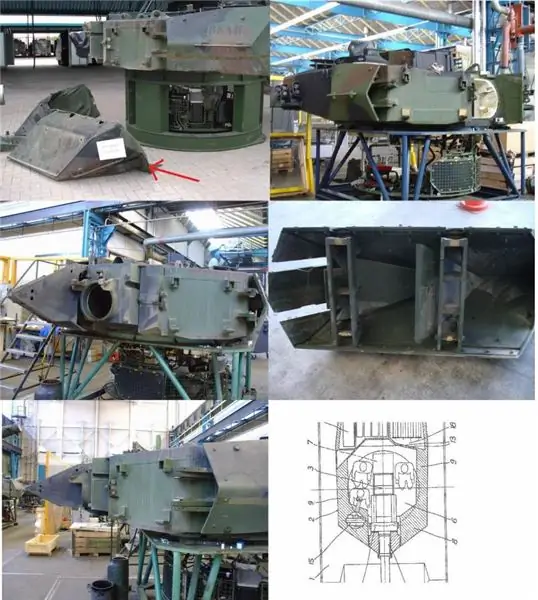
Armatura modulare con nanoceramica per il carro armato LEOPARD 2
Contributo dell'armatura composita
Sebbene le tecnologie di protezione, che sono una combinazione di strati di metallo, compositi polimerici rinforzati con fibre e ceramica, siano ben consolidate, l'industria continua a sviluppare materiali compositi sempre più complessi, ma molti dei dettagli di questo processo sono accuratamente nascosti. Morgan Advanced Materials è ben noto nel settore, annunciando un premio alla conferenza Armored Vehicles XV a Londra lo scorso anno per la sua tecnologia di difesa SAMAS. Secondo Morgan, la protezione SAMAS ampiamente utilizzata sui veicoli dell'esercito britannico è un materiale composito rinforzato con materiali come S-2 Glass, E-Glass, aramide e polietilene, quindi formato in fogli e polimerizzato ad alta pressione: “Le fibre possono essere combinate con materiali ibridi ceramica-metallo per soddisfare particolari requisiti di design e prestazioni."
Secondo Morgan, l'armatura SAMAS con uno spessore totale di 25 mm, utilizzata per la produzione di capsule protettive dell'equipaggio, può ridurre il peso dei veicoli leggeri protetti di oltre 1000 kg rispetto ai veicoli con una capsula in acciaio. Altri vantaggi includono riparazioni più semplici con spessori inferiori a 5 mm e le proprietà intrinseche del rivestimento antischeggia di questo materiale.
Progressi espliciti dello spinello
Secondo l'US Navy Research Laboratory, lo sviluppo e la produzione di materiali trasparenti a base di ossido di magnesio e alluminio (MgAI2O4), noti anche collettivamente come spinelli artificiali, è in piena espansione. Gli spinelli sono noti da tempo non solo per la loro forza - lo spinello spesso 0,25 "ha le stesse caratteristiche balistiche del vetro antiproiettile da 2,5" - ma anche per la difficoltà di realizzare parti di grandi dimensioni con trasparenza uniforme. Tuttavia, un gruppo di scienziati di questo laboratorio ha inventato un nuovo processo per la sinterizzazione a bassa temperatura nel vuoto, che consente di ottenere parti con dimensioni limitate solo dalle dimensioni della pressa. Si tratta di un importante passo avanti rispetto ai precedenti processi di produzione, che iniziavano con il processo di fusione della polvere originale in un crogiolo di fusione.
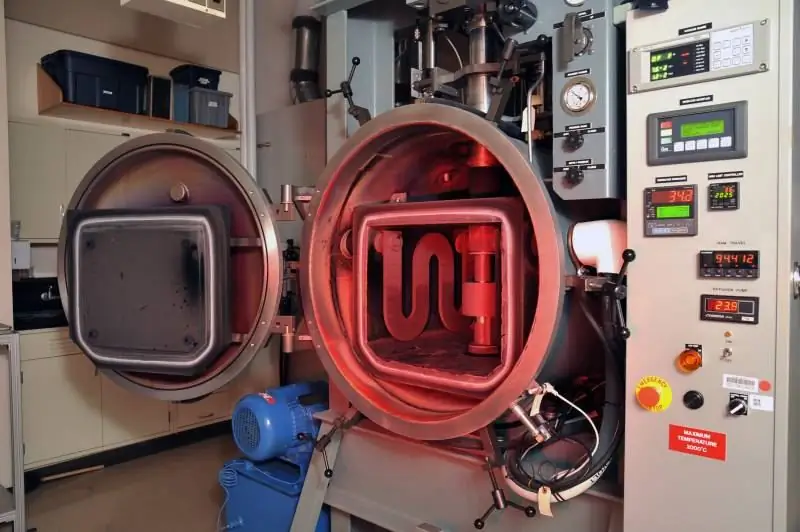
Uno dei segreti del nuovo processo è la distribuzione uniforme dell'additivo per sinterizzazione al fluoruro di litio (LiF), che fonde e lubrifica i grani di spinello in modo che possano essere distribuiti uniformemente durante la sinterizzazione. Invece di miscelare a secco fluoruro di litio e polveri di spinello, il laboratorio ha sviluppato un metodo per rivestire uniformemente le particelle di spinello con fluoruro di litio. Ciò consente di ridurre significativamente il consumo di LiF e aumentare la trasmissione luminosa fino al 99% del valore teorico nelle regioni dello spettro visibile e medio infrarosso (0,4-5 micron).
Il nuovo processo, che consente la produzione di ottiche in varie forme, compresi i fogli che si adattano comodamente alle ali di un aereo o di un drone, è stato concesso in licenza da una società anonima. Le possibili applicazioni per lo spinello includono vetro corazzato che pesa meno della metà della massa del vetro esistente, maschere protettive per soldati, ottiche per laser di nuova generazione e occhiali per sensori multispettrali. Quando si producono in serie, ad esempio, occhiali resistenti alle crepe per smartphone e tablet, il costo dei prodotti in spinello diminuirà in modo significativo.
PERLUCOR - una nuova pietra miliare nei sistemi di protezione dai proiettili e dall'usura
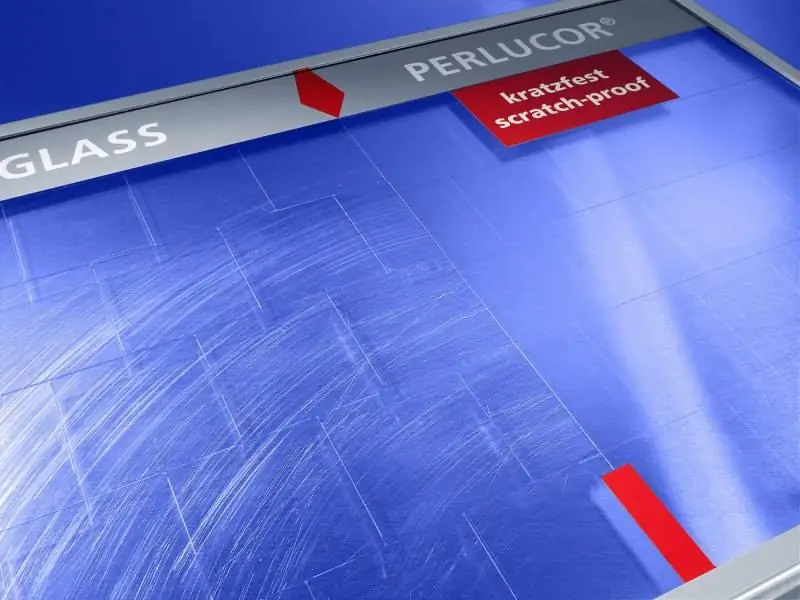
CeramTec-ETEC ha sviluppato la ceramica trasparente PERLUCOR alcuni anni fa con buone prospettive sia per la difesa che per le applicazioni civili. Le eccellenti proprietà fisiche, chimiche e meccaniche di PERLUCOR sono state le ragioni principali del successo dell'ingresso nel mercato di questo materiale.
PERLUCOR ha una trasparenza relativa di oltre il 90%, è da tre a quattro volte più resistente e più duro del vetro ordinario, la resistenza al calore di questo materiale è circa tre volte superiore, il che ne consente l'utilizzo a temperature fino a 1600°C, inoltre ha un'altissima resistenza chimica, questo ne permette l'utilizzo con acidi e alcali concentrati. PERLUCOR ha un alto indice di rifrazione (1, 72), che consente di fabbricare obiettivi ottici ed elementi ottici di dimensioni miniaturizzate, ovvero ottenere dispositivi con un potente ingrandimento, che non è possibile ottenere con polimeri o vetro. Le piastrelle di ceramica PERLUCOR hanno un formato standard di 90x90 mm; CeramTec-ETEC ha però sviluppato una tecnologia per la produzione di lastre di forma complessa basata su questo formato secondo le specifiche del cliente. Lo spessore dei pannelli può essere in casi speciali di decimi di millimetro, ma, di regola, è di 2-10 mm.
Lo sviluppo di sistemi di protezione trasparente più leggeri e sottili per il mercato della difesa sta procedendo a ritmo sostenuto. Un contributo significativo a questo processo è dato dalla ceramica trasparente dell'azienda SegamTes, che fa parte dei sistemi di protezione di molti produttori. Quando testato secondo STANAG 4569 o APSD, la riduzione del peso è dell'ordine del 30-60 percento.
Negli ultimi anni ha preso forma un'altra direzione nello sviluppo delle tecnologie sviluppate da SegatTes-ETEC. I finestrini dei veicoli, specialmente nelle aree rocciose e desertiche come l'Afghanistan, sono soggetti a urti e graffi dovuti al movimento delle spazzole dei tergicristalli su un parabrezza sabbioso e polveroso. Inoltre, le caratteristiche balistiche degli occhiali antiproiettile che sono stati danneggiati dai colpi di pietra sono ridotte. Durante le ostilità, i veicoli con vetri danneggiati sono esposti a rischi gravi e imprevedibili. SegamTes-ETEC ha sviluppato una soluzione davvero innovativa e originale per proteggere il vetro da questo tipo di usura. Uno strato sottile (<1 mm) di rivestimento ceramico PERLUCOR sulla superficie del parabrezza aiuta a resistere con successo a tali danni. Questa protezione è adatta anche per strumenti ottici come telescopi, lenti, apparecchiature a infrarossi e altri sensori. Le lenti piatte e curve realizzate in ceramica trasparente PERLUCOR prolungano la durata di questa apparecchiatura ottica di grande valore e sensibilità.
CeramTec-ETEC ha presentato con successo un pannello per porta in vetro antiproiettile e un pannello protettivo resistente ai graffi e alla pietra al DSEI 2015 di Londra.
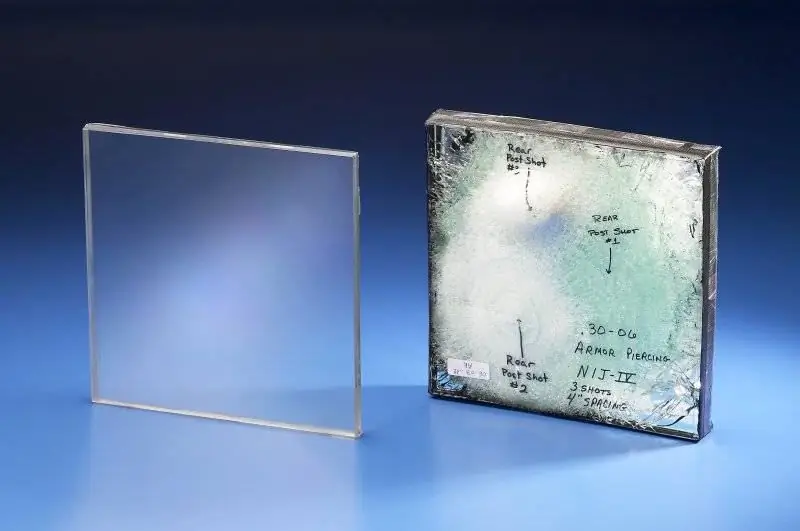
Nanoceramica resistente e flessibile
Flessibilità e resilienza non sono qualità insite nella ceramica, ma un team di scienziati guidato dalla professoressa di scienza dei materiali e meccanica Julia Greer del California Institute of Technology ha affrontato il problema. I ricercatori descrivono il nuovo materiale come "nanolattici ceramici tridimensionali resistenti, leggeri e rigenerabili". Tuttavia, questo è lo stesso nome di un articolo pubblicato da Greer e dai suoi studenti su una rivista scientifica un paio di anni fa.
Ciò che è nascosto sotto è meglio illustrato da un cubo di nanoreticoli di ossido di alluminio di diverse decine di micron, ripreso con un microscopio elettronico. Sotto l'azione del carico, si restringe dell'85% e, quando viene rimosso, viene riportato alla sua dimensione originale. Sono stati inoltre condotti esperimenti con reticoli costituiti da tubi di diverso spessore, dove i tubi più sottili sono i più resistenti ed elastici. Con uno spessore della parete del tubo di 50 nanometri, il reticolo è crollato e con uno spessore della parete di 10 nanometri è tornato al suo stato originale, un esempio di come l'effetto delle dimensioni aumenti la resistenza di alcuni materiali. La teoria spiega questo con il fatto che con una diminuzione delle dimensioni, il numero di difetti nei materiali sfusi diminuisce proporzionalmente. Con questa architettura del reticolo di tubi cavi, il 99,9% del volume del cubo è aria.
Il team del professor Greer crea queste minuscole strutture eseguendo un processo simile alla stampa 3D. Ogni processo inizia con un file CAD che guida due laser che "dipingono" la struttura in tre dimensioni, polimerizzando il polimero nei punti in cui i raggi si amplificano a vicenda in fase. Il polimero non polimerizzato fuoriesce dalla griglia polimerizzata, che ora diventa il substrato per formare la struttura finale. I ricercatori applicano quindi l'allumina al substrato utilizzando un metodo che controlla accuratamente lo spessore del rivestimento. Infine, le estremità del reticolo vengono tagliate per rimuovere il polimero, lasciando solo il reticolo cristallino dei tubi cavi di allumina.
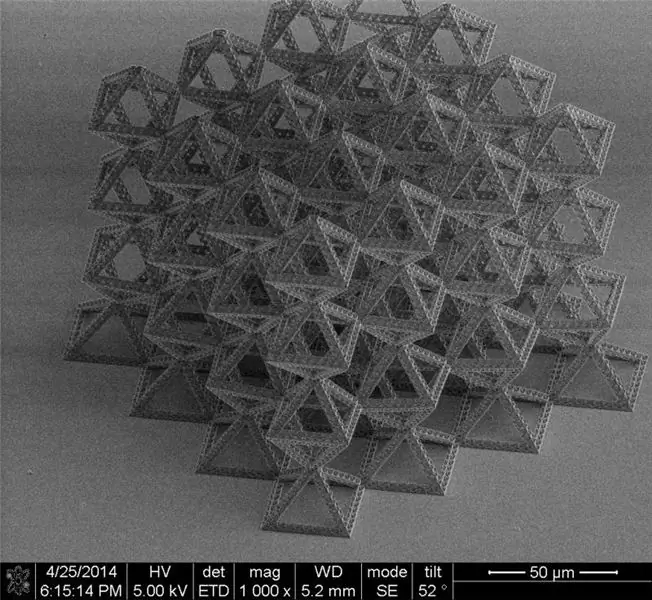
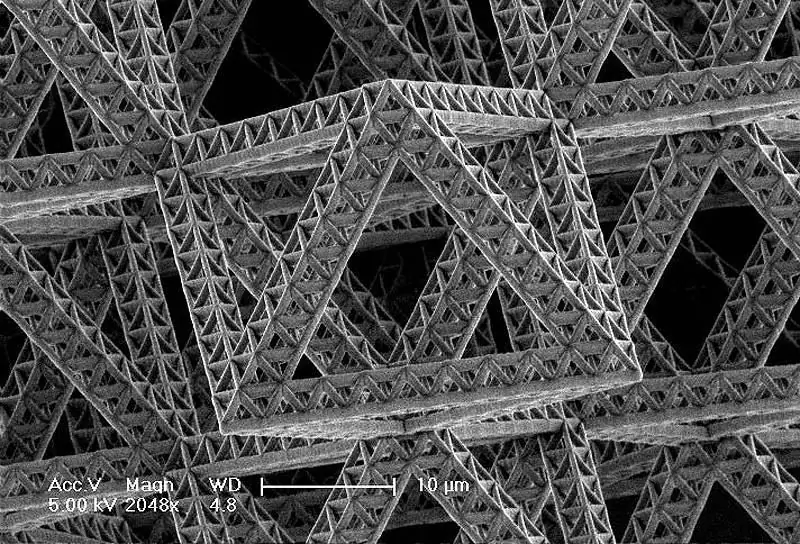
Forza dell'acciaio, ma pesa come l'aria
Il potenziale di tali materiali "ingegnerizzati", che sono per lo più aria in volume, ma sono meno resistenti dell'acciaio, è enorme, ma difficile da comprendere, quindi il professor Greer ha fornito diversi esempi eclatanti. Il primo esempio, palloncini da cui viene pompato l'elio, ma allo stesso tempo mantengono la loro forma. Il secondo, futuro aereo, il cui design pesa tanto quanto pesa il suo modello manuale. Sorprendentemente, se il famoso Golden Gate Bridge fosse fatto di tali nanoreticoli, tutti i materiali necessari per la sua costruzione potrebbero essere collocati (esclusa l'aria) su un palmo umano.
Proprio come gli enormi vantaggi strutturali di questi materiali robusti, leggeri e resistenti al calore adatti a innumerevoli applicazioni militari, le loro proprietà elettriche predeterminate potrebbero rivoluzionare l'immagazzinamento e la generazione di energia: “Queste nanostrutture sono molto leggere, meccanicamente stabili e allo stesso tempo enormi in dimensioni superfici, cioè possiamo utilizzare in una varietà di applicazioni di tipo elettrochimico."
Questi includono elettrodi estremamente efficienti per batterie e celle a combustibile, sono un obiettivo prezioso per alimentatori autonomi, centrali elettriche portatili e trasportabili, nonché una vera svolta nella tecnologia delle celle solari.
"Anche i cristalli fotonici possono essere nominati in questo senso", ha detto Greer. "Queste strutture ti consentono di manipolare la luce in modo tale da poterla catturare completamente, il che significa che puoi realizzare celle solari molto più efficienti: catturi tutta la luce e non hai perdita di riflessione".
"Tutto ciò suggerisce che la combinazione dell'effetto dimensione nei nanomateriali e negli elementi strutturali ci consente di creare nuove classi di materiali con proprietà che non sono state ottenibili", ha affermato il professor Greer presso l'Organizzazione europea per la ricerca nucleare in Svizzera. "La sfida più grande che dobbiamo affrontare è come scalare e passare dal nano alla dimensione del nostro mondo".
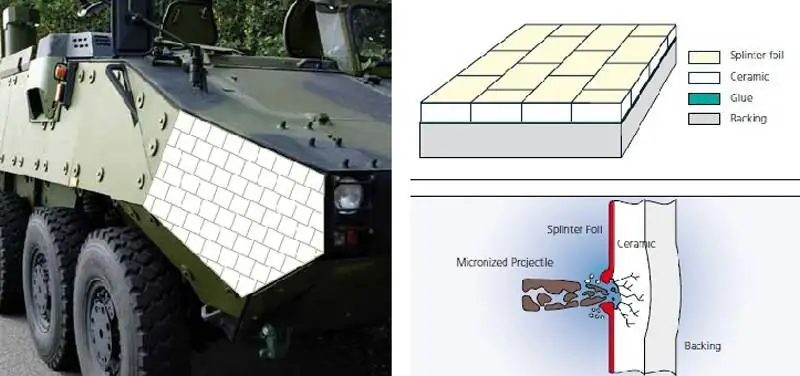
Protezione in ceramica trasparente industriale
IBD Deisenroth Engineering ha sviluppato un'armatura in ceramica trasparente con prestazioni balistiche paragonabili all'armatura in ceramica opaca. Questa nuova armatura trasparente è circa il 70% più leggera del vetro blindato e può essere assemblata in strutture con le stesse caratteristiche multi-impatto (capacità di resistere a più colpi) dell'armatura opaca. Ciò consente non solo di ridurre drasticamente la massa dei veicoli con grandi finestre, ma anche di chiudere tutti i vuoti balistici.
Per ottenere una protezione secondo STANAG 4569 Livello 3, il vetro antiproiettile ha una densità superficiale di circa 200 kg/m2. Con un'area tipica della finestra di un camion di tre metri quadrati, la massa dei vetri antiproiettile sarà di 600 kg. Quando si sostituiscono tali occhiali antiproiettile con ceramiche IBD, la riduzione di peso sarà di oltre 400 kg. La ceramica trasparente di IBD è un ulteriore sviluppo della ceramica IBD NANOTech. IBD è riuscita a sviluppare processi di incollaggio speciali che vengono utilizzati per assemblare piastrelle di ceramica ("armatura trasparente a mosaico") e quindi laminare questi assemblaggi su strati strutturali resistenti per formare grandi pannelli per finestre. Grazie alle eccezionali caratteristiche di questo materiale ceramico, è possibile produrre pannelli corazzati trasparenti con un peso notevolmente inferiore. Il supporto, in combinazione con il laminato Natural NANO-Fiber, migliora ulteriormente le prestazioni balistiche della nuova protezione trasparente grazie al suo maggiore assorbimento di energia.
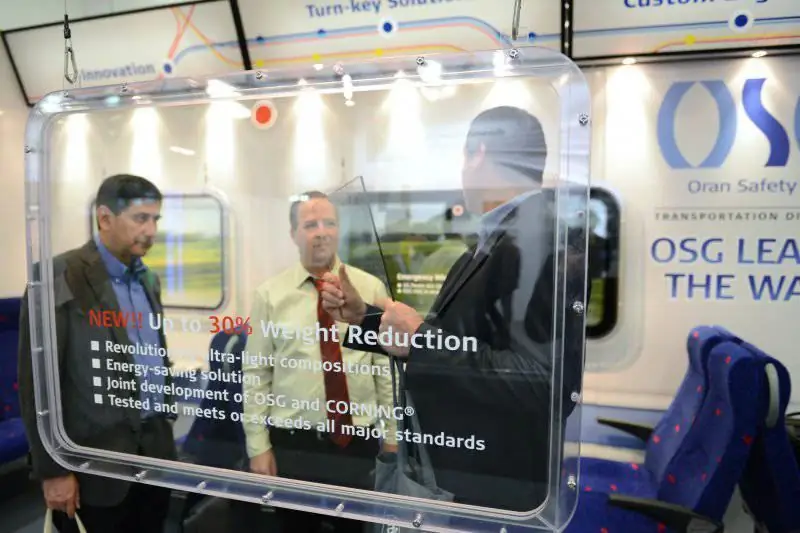
L'azienda israeliana OSG (Oran Safety Glass), rispondendo ai crescenti livelli di instabilità e tensione in tutto il mondo, ha sviluppato una vasta gamma di prodotti in vetro antiproiettile. Sono progettati specificamente per i settori della difesa e civile, militare, paramilitare, occupazioni civili ad alto rischio, edilizia e industria automobilistica. L'azienda promuove sul mercato le seguenti tecnologie: soluzioni di protezione trasparente, soluzioni di protezione balistica, ulteriori sistemi avanzati di armatura trasparente, finestre con visualizzazione digitale, finestre per uscite di emergenza, finestre in ceramica con tecnologia di visualizzazione a colori, sistemi di indicatori luminosi integrati, scudi in vetro antiurto., e, infine, la tecnologia antischeggia ADI.
I materiali trasparenti OSG sono costantemente testati in situazioni di vita reale: respingono attacchi fisici e balistici, salvano vite e proteggono la proprietà. Tutti i materiali trasparenti blindati sono stati realizzati secondo i principali standard internazionali.