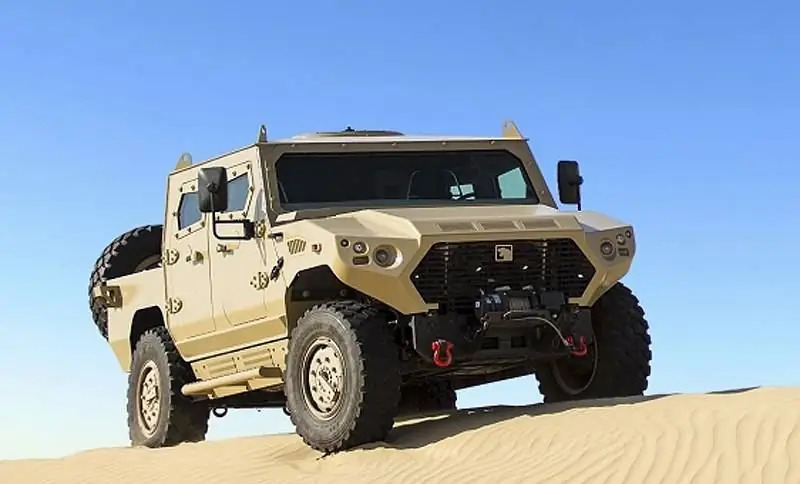
L'armatura è di milioni di anni più vecchia dell'umanità e si è sviluppata principalmente per proteggere da mascelle e artigli. È possibile che coccodrilli e tartarughe possano in parte ispirare gli umani a creare elementi protettivi. Tutte le armi di energia cinetica, che si tratti di una mazza preistorica o di un proiettile perforante, sono progettate per concentrare una grande forza in una piccola area, il suo compito è penetrare nel bersaglio e infliggergli il massimo danno. Di conseguenza, il compito dell'armatura è prevenire ciò deviando o distruggendo i mezzi attaccanti e/o disperdendo l'energia d'impatto su un'area il più ampia possibile al fine di ridurre al minimo eventuali danni alla manodopera, ai sistemi di trasporto e alle strutture che protegge.
L'armatura moderna consiste tipicamente in uno strato esterno duro per fermare, deviare o distruggere il proiettile, uno strato intermedio con un "lavoro da rompere" molto alto e uno strato interno viscoso per prevenire crepe e detriti.
Acciaio
L'acciaio, che è diventato il primo materiale ampiamente utilizzato nella creazione di veicoli blindati, è ancora richiesto, nonostante l'emergere di armature a base di leghe leggere di alluminio e titanio, ceramica, compositi a matrice polimerica, rinforzati con fibre di vetro, aramide e polietilene ad altissimo peso molecolare, nonché materiali compositi a matrice metallica.
Molte acciaierie, tra cui SSAB, continuano a sviluppare acciai altoresistenziali per una varietà di applicazioni critiche dal punto di vista del peso come guaine aggiuntive. L'acciaio corazzato ARM OX 600T, disponibile negli spessori di 4-20 mm, è disponibile con una durezza garantita da 570 a 640 unità HBW (abbreviazione di Durezza, Brinell, Wolfram; un test in cui viene pressata una sfera di tungsteno di diametro standard in un campione di materiale di forza nota, si misura il diametro dell'incavo formato, poi si sostituiscono questi parametri nella formula, che permette di ottenere il numero di unità di durezza).
SSAB sottolinea inoltre l'importanza di raggiungere il giusto equilibrio tra durezza e tenacità per la protezione da penetrazione e scoppio. Come tutti gli acciai, ARMOX 600T è composto da ferro, carbonio e una serie di altri componenti di lega tra cui silicio, manganese, fosforo, zolfo, cromo, nichel, molibdeno e boro.
Ci sono limitazioni alle tecniche di produzione utilizzate, soprattutto quando si tratta di temperatura. Questo acciaio non è destinato a trattamenti termici aggiuntivi; se riscaldato oltre i 170°C dopo la consegna, SSAB non può garantirne le proprietà. È probabile che le aziende che possono aggirare questo tipo di restrizione attirino l'attento esame dei produttori di veicoli blindati.
Un'altra azienda svedese, Deform, offre parti stampate a caldo in acciaio per armature antiproiettile ai produttori di veicoli corazzati, in particolare a coloro che desiderano migliorare la protezione dei veicoli commerciali/civili.
I firewall Deform monoblocco sono installati nella Nissan PATROL 4x4, nel minibus Volkswagen T6 TRANSPORTER e nel pick-up Isuzu D-MAX, insieme a un solido pavimento in lamiera dello stesso materiale. Il processo di formatura a caldo sviluppato da Deform e utilizzato nella produzione di lastre mantiene una durezza di 600 HB [HBW].
L'azienda sostiene di poter ripristinare le proprietà di tutti gli acciai per armature presenti sul mercato mantenendo una forma strutturalmente definita, mentre le parti risultanti sono di gran lunga superiori alle tradizionali strutture saldate e parzialmente sovrapposte. Nel metodo sviluppato da Deform, le lastre vengono bonificate dopo lo stampaggio a caldo. Grazie a questo processo è possibile ottenere forme tridimensionali non ottenibili mediante stampaggio a freddo senza l'obbligo in tali casi di "saldature che violino l'integrità dei punti critici".
Lamiere di acciaio deformate a caldo sono state utilizzate su BAE Systems BVS-10 e CV90 e, dall'inizio degli anni '90, su molte macchine Kraus-Maffei Wegmann (KMW). Stanno arrivando gli ordini per la produzione di corazze tridimensionali per il carro armato LEOPARD 2 e diverse lamiere sagomate per i veicoli BOXER e PUMA, oltre a diversi veicoli Rheinmetall, tra cui ancora il BOXER, nonché un portello per il veicolo WIESEL. Deform funziona anche con altri materiali protettivi tra cui alluminio, kevlar/aramide e titanio.
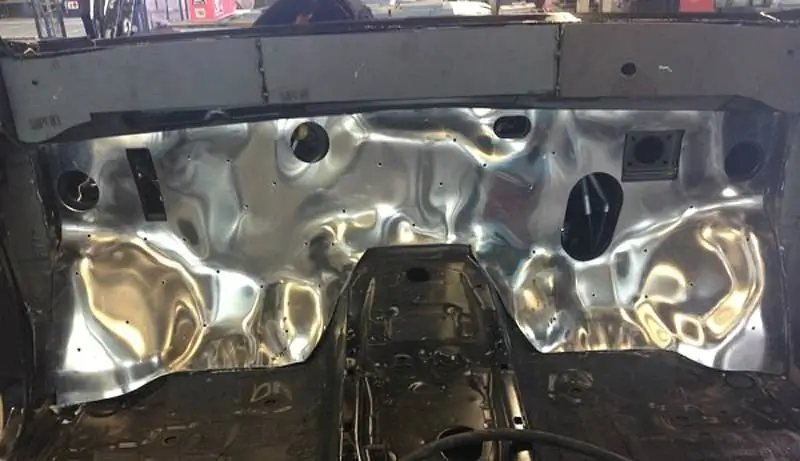
Progresso in alluminio
Per quanto riguarda i veicoli corazzati, per la prima volta l'armatura in alluminio è stata ampiamente utilizzata nella produzione del veicolo corazzato M113, prodotto dal 1960. Era una lega, denominata 5083, contenente il 4,5% di magnesio e quantità molto minori di manganese, ferro, rame, carbonio, zinco, cromo, titanio e altri. Sebbene 5083 mantenga bene la sua resistenza dopo la saldatura, non è una lega trattabile termicamente. Non ha una buona resistenza ai proiettili perforanti da 7,62 mm, ma, come hanno confermato i test ufficiali, blocca i proiettili perforanti di stile sovietico da 14,5 mm meglio dell'acciaio, risparmiando peso e aggiungendo la forza desiderata. Per questo livello di protezione, la lamiera di alluminio è più spessa e 9 volte più resistente dell'acciaio con una densità inferiore di 265 r/cm3, che si traduce in una riduzione del peso della struttura.
I produttori di veicoli corazzati iniziarono presto a richiedere armature in alluminio più leggere, balisticamente più resistenti, saldabili e trattabili termicamente, il che portò allo sviluppo di Alcan del 7039 e successivamente del 7017, entrambi con un contenuto di zinco più elevato.
Come per l'acciaio, lo stampaggio e il successivo assemblaggio possono influire negativamente sulle proprietà protettive dell'alluminio. Durante la saldatura, le zone colpite dal calore si ammorbidiscono, ma la loro resistenza viene parzialmente ripristinata a causa dell'indurimento durante l'invecchiamento naturale. La struttura del metallo si modifica in zone ristrette in prossimità della saldatura, creando grosse sollecitazioni residue in caso di errori di saldatura e/o di montaggio. Di conseguenza, le tecniche di produzione dovrebbero minimizzarli, mentre dovrebbe essere minimizzato anche il rischio di tensocorrosione, specialmente quando si prevede che la vita di progetto della macchina sia superiore a tre decenni.
La tensocorrosione è un processo di comparsa e crescita di cricche in un ambiente corrosivo, che tende a deteriorarsi all'aumentare del numero di elementi di lega. La formazione di cricche e la loro successiva crescita avviene per diffusione dell'idrogeno lungo i bordi dei grani.
La determinazione della suscettibilità alla fessurazione inizia con l'estrazione di una piccola quantità di elettrolita dalle fessure e la sua analisi. Vengono eseguiti test di corrosione sotto sforzo a bassa velocità di deformazione per determinare quanto gravemente è stata danneggiata una particolare lega. L'allungamento meccanico di due campioni (uno in un ambiente corrosivo e l'altro in aria secca) si verifica fino a quando non si guastano, quindi viene confrontata la deformazione plastica nel sito di frattura: più il campione viene allungato fino al cedimento, meglio è.
La resistenza alla tensocorrosione può essere migliorata durante la lavorazione. Ad esempio, secondo Total Materia, che si definisce "il più grande database di materiali al mondo", Alcan ha migliorato di 40 volte le prestazioni del 7017 nei test di tensocorrosione accelerata. I risultati ottenuti consentono inoltre di sviluppare metodi di protezione dalla corrosione per zone di strutture saldate, in cui è difficile evitare tensioni residue. Proseguono le ricerche volte al miglioramento delle leghe al fine di ottimizzare le caratteristiche elettrochimiche dei giunti saldati. Il lavoro sulle nuove leghe trattabili termicamente si concentra sul miglioramento della loro resistenza e resistenza alla corrosione, mentre il lavoro sulle leghe non trattabili mira a rimuovere i vincoli imposti dai requisiti di saldabilità. I materiali più resistenti in fase di sviluppo saranno il 50% più resistenti delle migliori armature in alluminio in uso oggi.
Le leghe a bassa densità come l'alluminio al litio offrono un risparmio di peso di circa il 10% rispetto alle leghe precedenti con resistenza ai proiettili comparabile, sebbene le prestazioni balistiche debbano ancora essere completamente valutate secondo Total Materia.
Anche i metodi di saldatura, compresi quelli robotici, stanno migliorando. Tra i compiti da risolvere ci sono la minimizzazione della fornitura di calore, un arco di saldatura più stabile grazie al miglioramento dei sistemi di alimentazione dell'energia e del filo, nonché il monitoraggio e il controllo del processo da parte di sistemi esperti.
MTL Advanced Materials ha collaborato con ALCOA Defense, un rinomato produttore di piastre corazzate in alluminio, per sviluppare quello che l'azienda descrive come un "processo di formatura a freddo affidabile e ripetibile". L'azienda osserva che le leghe di alluminio sviluppate per le applicazioni delle armature non sono state progettate per la formatura a freddo, il che significa che il suo nuovo processo dovrebbe aiutare a evitare le comuni modalità di guasto, inclusa la fessurazione. L'obiettivo finale è consentire ai progettisti di macchine di ridurre al minimo la necessità di saldatura e il numero di parti, secondo l'azienda. Riducendo il volume della saldatura, sottolinea l'azienda, aumenta la resistenza strutturale e la protezione dell'equipaggio riducendo i costi di produzione. Partendo dalla collaudata lega 5083-H131, l'azienda ha sviluppato un processo per la formatura a freddo di parti con un angolo di piegatura di 90 gradi lungo e attraverso i grani, quindi è passata a materiali più complessi, ad esempio le leghe 7017, 7020 e 7085, ottenendo anche buoni risultati.
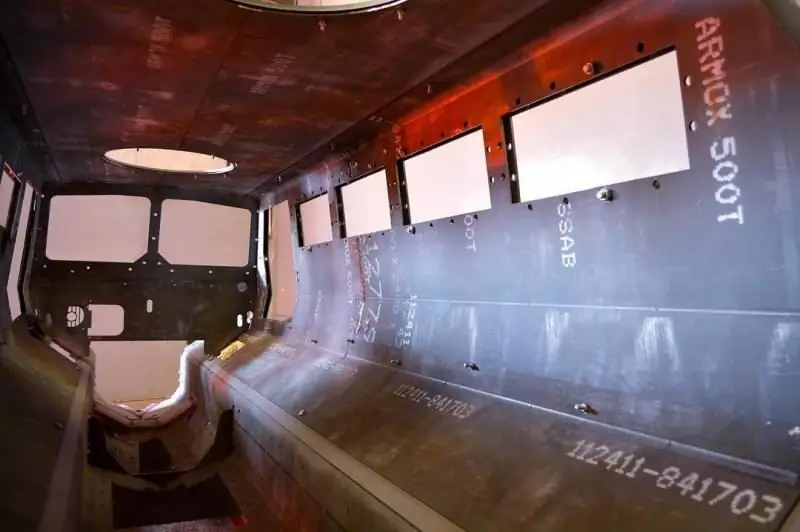
Ceramiche e compositi
Diversi anni fa, Morgan Advanced Materials ha annunciato lo sviluppo di diversi sistemi di armature SAMAS, che consistevano in una combinazione di ceramiche avanzate e compositi strutturali. La linea di prodotti comprende armature incernierate, rivestimenti anti-frammentazione, capsule di sopravvivenza realizzate in compositi strutturali per la sostituzione di scafi metallici e la protezione di moduli d'arma, sia abitati che disabitati. Tutti possono essere adattati a requisiti specifici o realizzati su ordinazione.
Fornisce protezione STANAG 4569 Livello 2-6, insieme a prestazioni multi-impatto e risparmio di peso (l'azienda afferma che questi sistemi pesano la metà di prodotti simili in acciaio) e si adattano a minacce, piattaforme e missioni specifiche. … I rivestimenti antischeggia possono essere realizzati da pannelli piani del peso di 12,3 kg per coprire una superficie di 0,36 m2 (circa 34 kg/m2) o raccordi pieni del peso di 12,8 kg per 0,55 m2 (circa 23,2 kg/m2).
Secondo Morgan Advanced Materials, l'armatura aggiuntiva progettata per il nuovo e l'ammodernamento delle piattaforme esistenti offre le stesse capacità a metà del peso. Il sistema brevettato fornisce la massima protezione contro un'ampia gamma di minacce, tra cui armi di piccolo e medio calibro, ordigni esplosivi improvvisati (IED) e granate con propulsione a razzo, nonché prestazioni multi-impatto.
Per i moduli d'arma viene offerto un sistema di armatura "semi-strutturale" con una buona resistenza alla corrosione (oltre alle applicazioni aeree e marittime), e oltre a ridurre il peso e ridurre al minimo i problemi con il centro di gravità, a differenza dell'acciaio, crea meno problemi di compatibilità elettromagnetica.
La protezione dei moduli delle armi è un problema particolare, poiché sono un bersaglio attraente, poiché la loro disattivazione compromette drasticamente il controllo della situazione da parte dell'equipaggio e la capacità del veicolo di affrontare le minacce vicine. Hanno anche un'optoelettronica delicata e motori elettrici vulnerabili. Poiché di solito sono installati nella parte superiore del veicolo, l'armatura dovrebbe essere leggera per mantenere il baricentro il più basso possibile.
Il sistema di protezione dei moduli delle armi, che può includere vetro blindato e protezione della parte superiore, è completamente abbattibile, due persone possono rimontarlo in 90 secondi. Le capsule composite per la sopravvivenza sono realizzate con ciò che l'azienda descrive come "materiali resistenti e formulazioni polimeriche unici", forniscono protezione dalle schegge e possono essere riparate sul campo.
Protezione del soldato
L'SPS (Soldier Protection System) sviluppato da 3M Ceradyne include caschi e inserti in giubbotto antiproiettile per l'Integrated Head Protection System (IHPS) e VTP (Vital Torso Protection) - componenti ESAPI (Enhanced Small Arms Protective Insert) - inserto migliorato per la protezione contro armi leggere) del sistema SPS.
I requisiti IHPS includono un peso più leggero, una protezione passiva dell'udito e una migliore protezione dagli impatti contundenti. Il sistema include anche accessori come un componente per proteggere la mascella inferiore di un soldato, una visiera protettiva, un supporto per occhiali per la visione notturna, guide per, ad esempio, torcia e fotocamera e protezione antiproiettile modulare aggiuntiva. Il contratto, del valore di oltre 7 milioni di dollari, prevede la fornitura di circa 5.300 caschi. Nel frattempo, oltre 30.000 kit ESAPI - inserti più leggeri per giubbotti antiproiettile - saranno consegnati nell'ambito del contratto da $ 36 milioni. La produzione di entrambi questi kit è iniziata nel 2017.
Sempre nell'ambito del programma SPS, KDH Defense ha selezionato i materiali SPECTRA SHIELD e GOLD SHIELD di Honeywell per cinque sottosistemi, compreso il sottosistema Torso and Extremity Protection (TEP) da fornire per il progetto SPS. Il sistema di protezione TEP è più leggero del 26%, il che riduce il peso del sistema SPS del 10%. KDH utilizzerà SPECTRA SHIELD, a base di fibra UHMWPE, e GOLD SHIELD, a base di fibre aramidiche, nei propri prodotti per questo sistema.
SPECTRA fibra
Honeywell utilizza un processo proprietario di filatura e trafilatura della fibra polimerica per incorporare la materia prima UHMWPE nella fibra SPECTRA. Questo materiale è 10 volte più resistente dell'acciaio in termini di peso, la sua resistenza specifica è del 40% superiore a quella della fibra aramidica, ha un punto di fusione più alto del polietilene standard (150°C) e una maggiore resistenza all'usura rispetto ad altri polimeri, per esempio, poliestere.
Il materiale SPECTRA, forte e rigido, mostra un'elevata deformazione a rottura, cioè si allunga molto fortemente prima di rompersi; questa proprietà permette di assorbire una grande quantità di energia d'urto. Honeywell afferma che i compositi in fibra SPECTRA si comportano molto bene sotto impatti ad alta velocità come proiettili di fucile e onde d'urto. Secondo l'azienda, "La nostra fibra avanzata reagisce all'impatto rimuovendo rapidamente l'energia cinetica dalla zona di impatto … ha anche un buon smorzamento delle vibrazioni, una buona resistenza alle deformazioni ripetute ed eccellenti caratteristiche di attrito interno delle fibre insieme a un'eccellente resistenza agli agenti chimici, acqua e luce UV."
Nella sua tecnologia SHIELD, Honeywell stende fili paralleli di fibre e li unisce impregnandoli con una resina avanzata per creare un nastro unidirezionale. Quindi gli strati di questo nastro vengono posizionati trasversalmente agli angoli desiderati e ad una data temperatura e pressione, saldati in una struttura composita. Per applicazioni indossabili morbide, è laminato tra due strati di film trasparente sottile e flessibile. Poiché le fibre rimangono diritte e parallele, dissipano l'energia dell'impatto in modo più efficiente rispetto a se fossero tessute in un tessuto.
Short Bark Industries utilizza anche SPECTRA SHIELD nella guardia del corpo BCS (Ballistic Combat Shirt) per il sistema SPS TEP. Short Bark è specializzato in protezioni morbide, abbigliamento tattico e accessori.
Secondo Honeywell, i soldati hanno scelto elementi protettivi realizzati con questi materiali dopo aver dimostrato prestazioni superiori rispetto alle loro controparti in fibra aramidica.