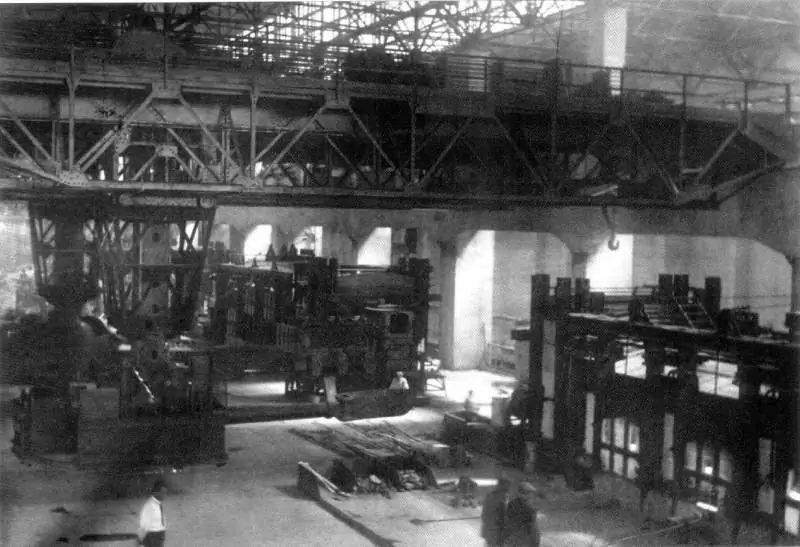
Risorsa strategica
È difficile sopravvalutare la produzione di acciaio di alta qualità per il complesso militare-industriale in condizioni di guerra. Questo è uno dei fattori più importanti per il successo degli eserciti sul campo di battaglia.
Come sapete, i metallurgisti di Krupp sono stati tra i primi a imparare a produrre acciaio di alta qualità per armi.
I tedeschi adottarono il processo di fabbricazione Thomas alla fine del XIX secolo. Questo metodo di fusione dell'acciaio ha permesso di rimuovere le impurità di fosforo dal minerale, aumentando automaticamente la qualità del prodotto. Armature di alta qualità e acciaio per armi durante la prima guerra mondiale spesso garantivano la superiorità dei tedeschi sul campo di battaglia.
Per organizzare una tale produzione, erano necessari nuovi materiali refrattari, che rivestivano le superfici interne dei forni. I tedeschi usavano i più recenti refrattari alla magnesite per il loro tempo, resistendo a temperature di oltre 2000 gradi. Tali sostanze di maggiore refrattarietà sono a base di ossidi di magnesio con piccole miscele di ossidi di alluminio.
All'inizio del XX secolo, i paesi con tecnologie per la produzione di massa di refrattari di magnesite potevano permettersi di produrre armature e canne di fucile di alta qualità. Questo può essere paragonato a un vantaggio strategico.
Più bassi in termini di resistenza al fuoco erano i cosiddetti materiali altamente refrattari che resistono a temperature da 1750 a 1950 gradi. Questi sono refrattari dolomite e ad alto contenuto di allumina. I materiali refrattari Fireclay, semi-acidi, quarzo e dinas possono resistere a temperature da 1610 a 1750 gradi.
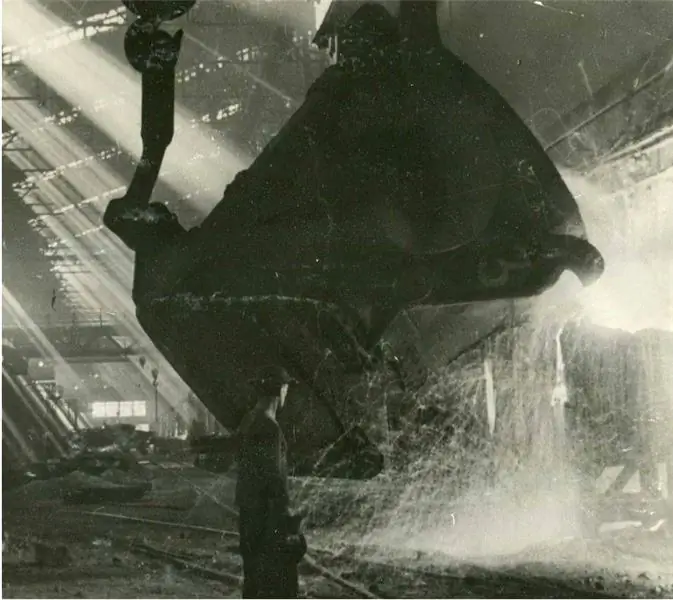
A proposito, le tecnologie e i siti per la produzione di refrattari di magnesite sono apparsi per la prima volta in Russia nel 1900.
Il mattone refrattario di magnesite Satka nel 1905 ricevette una medaglia d'oro all'Esposizione mondiale dell'industria di Liegi. È stato prodotto vicino a Chelyabinsk nella città di Satka, dove si trovava un deposito di magnesite unico.
Il minerale di periclasio, da cui sono stati realizzati i refrattari in fabbrica, era di alta qualità e non richiedeva un ulteriore arricchimento. Di conseguenza, il refrattario alla magnesite di Satka era superiore ai suoi omologhi della Grecia e dell'Austria.
Colmare il gap
Nonostante il mattone di magnesite di qualità piuttosto alta di Satka, fino agli anni '30, i principali materiali refrattari dei metallurgisti sovietici erano materiali dina dall'argilla. Naturalmente, ottenere una temperatura elevata per la fusione dell'acciaio per armi non ha funzionato: il rivestimento degli interni dei forni a focolare aperto si è sbriciolato e ha richiesto riparazioni straordinarie.
Non c'era abbastanza mattone Satka e nel periodo post-rivoluzionario le principali tecnologie di produzione andarono perse.
Allo stesso tempo, gli europei sono andati avanti: ad esempio, la magnesite austriaca Radex si è distinta per un'eccellente resistenza al fuoco.
L'Unione Sovietica ha acquistato questo materiale. Ma era impossibile ottenere un analogo senza un segreto di produzione. Questo problema è stato affrontato da un laureato dell'Università tecnica statale di Mosca. N. E. Bauman Alexey Petrovich Panarin. Nello stabilimento Magnet (ex Satka Combine) nel 1933 diresse il Central Plant Laboratory. E cinque anni dopo, ha lanciato la produzione in serie di refrattari periclasio-cromite o cromomagnesite per forni a focolare aperto.
Nello stabilimento metallurgico di Zlatoust e nella falce e martello di Mosca, il refrattario di Panarin ha sostituito i dina obsoleti.
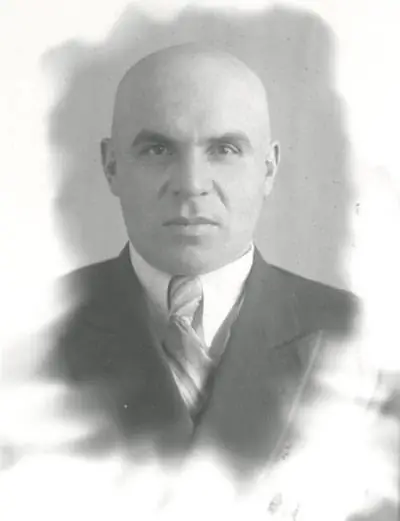
La tecnologia, che era stata sviluppata nel laboratorio di "Magnezit" per diversi anni, consisteva in una composizione e una dimensione delle particelle speciali.
In precedenza, l'impianto produceva mattoni di cromo-magnesite convenzionali, costituiti da magnesite e minerale di ferro di cromo, in un rapporto 50/50. Il segreto rivelato dal gruppo di Panarin era il seguente:
Se il minerale di cromite in grani granulometrici grossolani con un contenuto minimo di frazioni inferiori a 0,5 mm viene aggiunto a una normale carica di magnesite, anche con un'aggiunta del 10% di tale minerale, la stabilità termica del mattone aumenta notevolmente.
All'aumentare dell'aggiunta di minerale di cromite di granulometria grossolana, la stabilità del mattone cresce e raggiunge un massimo in un certo rapporto di componenti."
La cromite per il nuovo refrattario fu prelevata nella miniera di Saranovskoye e il periclasio continuò ad essere estratto a Satka.
Per confronto, un normale mattone di magnesite "pre-rivoluzionario" ha resistito a temperature 5-6 volte inferiori alla novità di Panarin.
Nell'impianto di fusione del rame di Kirovograd, il refrattario di cromo-magnesite nel tetto di un forno a riverbero ha resistito a temperature fino a 1550 gradi per 151 giorni. In precedenza, i refrattari in tali forni dovevano essere cambiati ogni 20-30 giorni.
Nel 1941 fu dominata la produzione di refrattari su larga scala, che rese possibile l'utilizzo dei materiali in grandi forni per la produzione di acciaio a temperature fino a 1800 gradi. Un importante contributo a questo è stato dato dal direttore tecnico di "Magnezit" Alexander Frenkel, che ha sviluppato un nuovo metodo per fissare il materiale refrattario ai tetti dei forni.
Refrattari per la vittoria
Alla fine del 1941, i metallurgisti di Magnitka realizzarono l'impensabile prima: per la prima volta nella storia padroneggiarono la fusione dell'acciaio per armature per i carri armati T-34 nei principali forni pesanti a focolare aperto.
Il principale fornitore di refrattari per un processo così importante era Satka "Magnezit". Non è necessario parlare delle difficoltà del tempo di guerra, quando un terzo degli operai della fabbrica è stato chiamato al fronte e lo stato ha chiesto che il piano fosse superato. Tuttavia, l'impianto stava facendo il suo lavoro, e Panarin nel 1943
"Per padroneggiare la produzione di prodotti altamente refrattari da materie prime locali per la metallurgia ferrosa"
ricevette il Premio Stalin.
Nel 1944, questo ricercatore metallurgico svilupperà una tecnologia per la produzione di polvere di magnesite di alta qualità "Extra". Questo semilavorato è stato utilizzato per preparare un refrattario pressato utilizzato nella produzione particolarmente importante di acciaio corazzato nei forni elettrici. Il limite di temperatura per tali refrattari ha raggiunto i 2000 gradi.
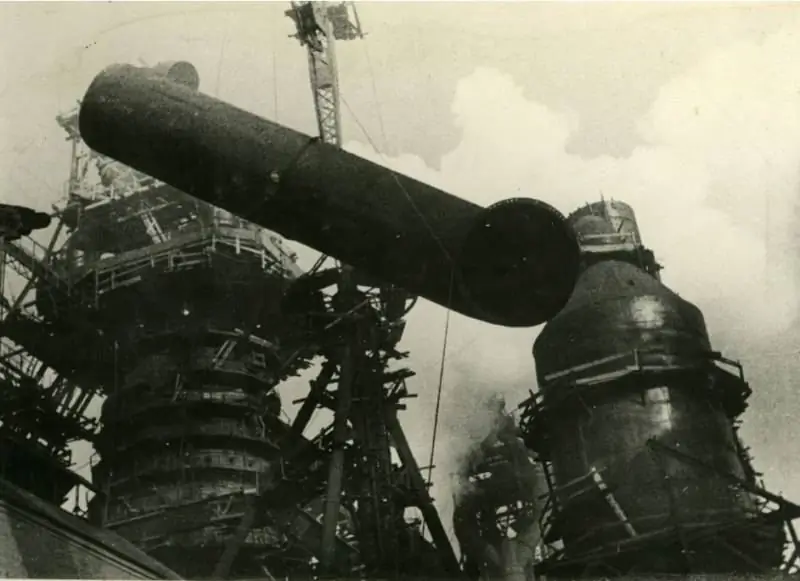
Ma non si dovrebbe presumere che l'esempio di un impianto di Magnesit generalmente di successo si estendesse all'intera industria dei refrattari dell'Unione Sovietica.
Una situazione particolarmente difficile si sviluppò negli Urali, dove praticamente tutti gli edifici dei carri armati del paese furono evacuati nel 1941-1942.
Gli impianti metallurgici di Magnitogorsk e Novotagilsk sono stati riorientati alla produzione di armature, fornendo prodotti a Sverdlovsk Uralmash, Chelyabinsk "Tankograd" e all'impianto di serbatoi N. 183 di Nizhny Tagil. Allo stesso tempo, gli impianti metallurgici avevano la propria produzione di refrattari da materie prime locali.
Ad esempio, a Magnitka, l'impianto dinas-chamotte produceva 65-70 mila tonnellate di mattoni all'anno. Questo non bastava nemmeno alle proprie necessità, per non parlare delle forniture ad altre imprese.
Le prime difficoltà sorsero quando le fabbriche di serbatoi iniziarono a costruire i propri forni di riscaldamento e termici. La metallurgia degli Urali aveva già a malapena abbastanza refrattari, quindi la produzione di scafi delle fabbriche di carri armati richiedeva materiali di alta qualità per il rivestimento dei forni.
Non si parlava di refrattari alla cromomagnesite qui: questo materiale scarseggiava e veniva persino esportato in cambio dell'American Lend-Lease. Almeno questo è menzionato in una serie di fonti. Gli storici degli Urali scrivono che la costosa cromomagnesite di Panarin potrebbe andare all'estero in cambio di scarse ferroleghe per l'armatura dei carri armati. Ma non ci sono ancora prove dirette di questo.
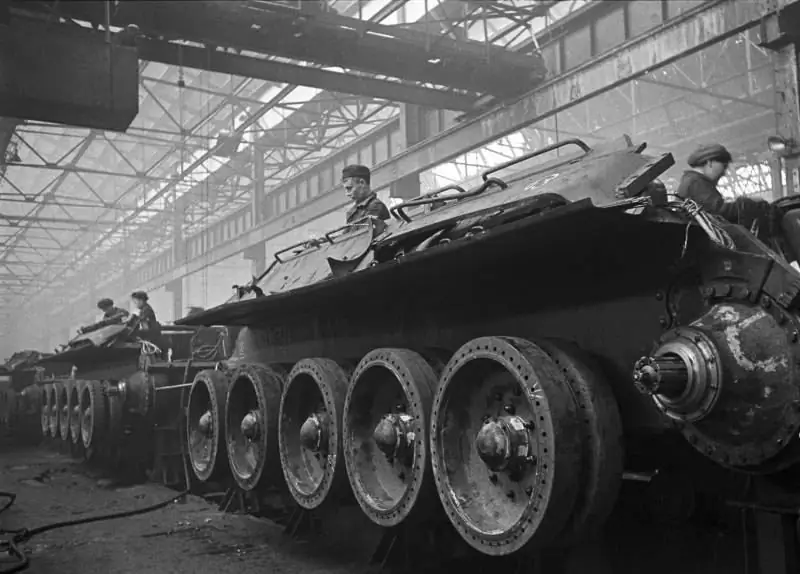
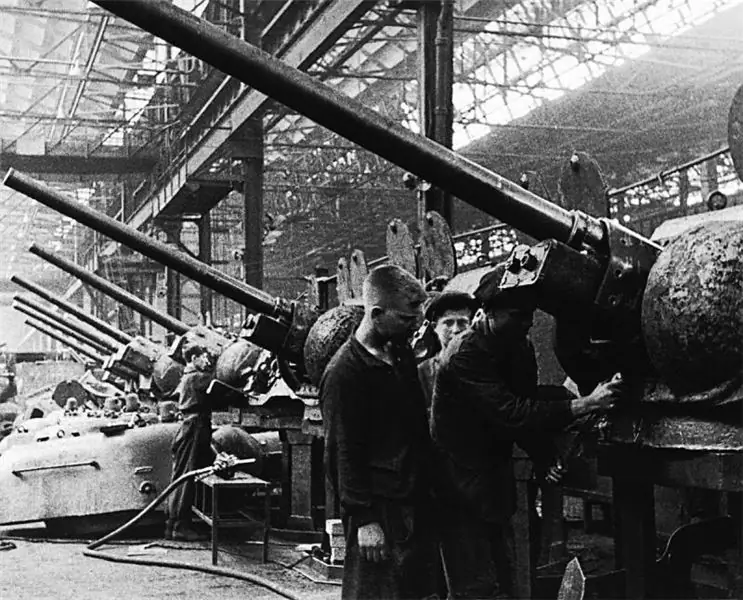
Le fabbriche di carri armati si affidavano principalmente al materiale refrattario dinas prodotto dallo stabilimento di Pervouralsk. Ma, in primo luogo, sono state prodotte solo 12 mila tonnellate al mese e, in secondo luogo, i metallurgisti hanno fatto la parte del leone.
L'espansione della produzione nello stabilimento di Pervouralsk è avvenuta molto lentamente. E a metà del 1942 apparvero solo 4 nuovi forni. Il resto o non era pronto o esisteva generalmente solo nei progetti.
I refrattari per i forni a focolare aperto delle fabbriche di serbatoi spesso erano di scarsa qualità, non completamente e nel momento sbagliato. Solo per la riparazione dei forni Uralmash nel quarto trimestre del 1942 furono necessarie 1035 tonnellate di mattoni resistenti al fuoco e furono ricevute solo circa 827 tonnellate.
Nel 1943, il negozio a focolare aperto di Uralmash, in generale, quasi si fermò a causa della mancanza di refrattari per la riparazione.
La qualità dei refrattari forniti durante la guerra lasciava molto a desiderare. Se in condizioni normali il mattone dina della fornace a focolare aperto poteva resistere a 400 calori, in tempo di guerra non superava i 135 calori. E nel marzo 1943, questo parametro era sceso a 30-40 manches.
Questa situazione dimostra chiaramente come la mancanza di una risorsa (in questo caso, refrattaria) possa rallentare seriamente il lavoro dell'intera industria della difesa. Come scrive il candidato alle scienze storiche Nikita Melnikov nelle sue opere, nel marzo 1943, tre forni a focolare aperto di Uralmash si fermarono ancora ed eseguirono un ciclo completo di lavori di riparazione. Ci sono volute 2346 tonnellate di dinas, 580 tonnellate di chamotte e 86 tonnellate di magnesite scarsa.
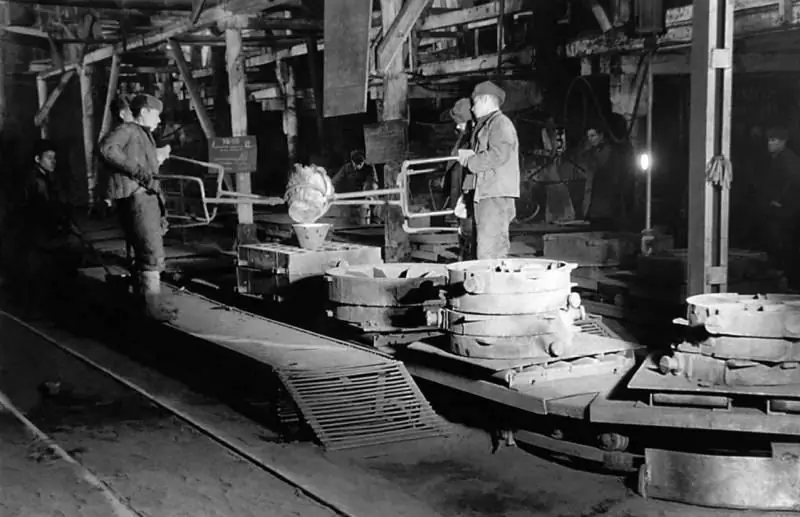
A metà del 1942, nello stabilimento di serbatoi n. 183, la situazione si stava sviluppando in modo simile: la produzione di acciaio era in ritardo rispetto all'assemblaggio meccanico. E abbiamo dovuto "importare" gli scafi T-34 da Uralmash.
Uno dei motivi era la mancanza di refrattari per la riparazione dei forni a focolare aperto, che nella primavera del 1942 funzionavano al limite. Di conseguenza, in autunno erano in funzione solo 2 forni a focolare aperto su 6. I volumi fusori furono ripristinati solo nella seconda metà del 1943.
La situazione con refrattari nella struttura del complesso di difesa sovietico durante la Grande Guerra Patriottica illustra chiaramente la complessità della situazione nella parte posteriore del paese.
Una carenza cronica di, in generale, non il prodotto più high-tech ha influito direttamente sul ritmo di produzione dei veicoli blindati.